Are your molds money pits?
Molds wear out. It’s inevitable. Constant use requires frequent replacements or repairs that result in maintenance, system downtime, and increased operational costs. Molds cost money, and that’s just the way it is–right?
There is, in fact, a better way to make more durable molds. It’s not really a secret, but it’s not how most moldmaking manufacturers go about things. For industries like blow and injection molding that chew through molds like they’re sticks of gum, it might be time to consider an alternative.
Enter advanced manufacturing. In a nutshell, it’s defined as the innovative technologies, processes, and techniques used to to enhance productivity, efficiency, and quality in the manufacturing industry. It includes fancy things like automation, robotics, artificial intelligence, additive manufacturing, and the Internet of Things.
In our case, we’re going to focus on how advanced manufacturing can improve mold durability through the use of alternative materials, design choices, and fabrication methods. We’ll also talk about some of the misconceptions around advanced manufacturing that might be stopping you from considering it as a viable option for your molds.
To set the scene, let’s zoom into precision mold components like pins, bushings, rollers, and rods. These little parts play supporting, yet indispensable, roles in industrial machinery. They keep systems aligned, moving, and ensure operations remain smooth. They can make or break the quality of a product.
In this post we’ll discuss how the little parts–specifically pins and bearings rollers–can cause issues that affect mold longevity. And we’ll provide advanced manufacturing solutions that help solve these problems, resulting in longer lasting molds that should hopefully not leave you questioning your life choices like Tom Hanks.
Issue 1: Mold pin misalignment
In both blow molding and injection molding, maintaining precise mold alignment is critical for achieving high-quality parts. Leader pins and guide bushings are necessary for proper mold alignment and closure, which prevents product defects, like flashing.
When pins become misaligned, mold adjustments or replacements are required, resulting in costly downtime and maintenance costs.
Why misalignment happens
Normal wear and tear is a major contributor to pin misalignment in both blow molding and injection molding. Constant use causes pins to degrade, especially in situations that involve a lot of sliding contact, corrosion, abrasion, or temperature cycling.
When pins wear down, they won’t fit snugly into their counterpart components. When this degradation happens precision is lost and misalignment occurs.
Hardened steels are well-suited for high-wear environments. But there are more suitable materials that can be used to create more durable pins that hold up better.
Improving pin performance with advanced materials
Advanced materials, like superalloys, can significantly improve the performance of mold components. You’ll get different advantages depending on the particular advanced material, some of which include:
- Superior wear resistance, which extends the life of components subject to continuous sliding contact.
- High-temperature stability, critical for applications like injection molds that undergo repeated heating and cooling cycles.
- Corrosion resistance, ideal for environments exposed to harsh chemicals or extreme temperatures.
- Abrasion resistance, when repeated sliding and striking can cause material to be worn away, or even when processing materials like glass fiber-reinforced polymers.
Although advanced materials may not be the traditional go-to material for pins, they offer a means of extending component life for molds that need few replacements or repair due to misalignment.
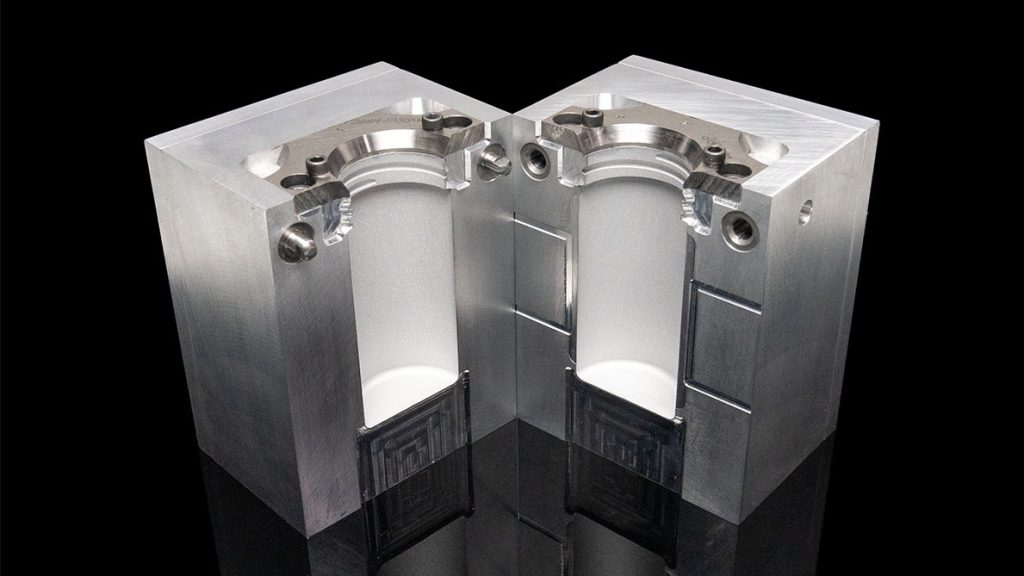
Image: Blow mold tool with guide pins and bushings made from hardened steel. © Hybrid CNC Parts.
Types of mold pins, durability issues, and material solutions
In injection and blow molds, there are several types of pins serving different functions. However, they all have something in common–wear. Here are a few common pin types, the main factors affecting their durability, and advanced material alternatives that would be better suited to longer-lasting components.
- Core pins
- Core pins form internal features in molded parts, like holes or cavities, and contact the material being molded. They need to be as wear resistant as possible.
- Issue: Sliding contact.
- Solution: With its excellent resistance to galling and adhesive wear, Stellite® 6 is a great option for maintaining core pin performance over longer production cycles, especially when sliding contact is a primary concern.
- Ejector Pins
- Ejector pins push the finished part out of the mold after it solidifies. They endure repeated contact and sliding, and when damaged. can result in incomplete ejection or part damage.
- Issue: Wear and thermal cycling.
- Solution: Superalloys that offer enhanced resistance to thermal cycling and wear, like Inconel® 718 or Stellite 6, would provide ejector pins with longer, more consistent lifecycles.
- Leader Pins and Guide Bushings
- Leader pins guide the mold halves into alignment during closure, while guide bushings support the movement of these pins, preventing misalignment.
- Issue: Corrosion and thermal cycling.
- Solution: In environments with high thermal cycling or corrosive conditions – such as with the constant heating and cooling during injection molding – Inconel 718 can offer better long-term performance due to its superior resistance to oxidation and corrosion, whereas M2 high speed tool steel excels in high-wear, high-load scenarios.
Issue 2: Bearing failure in molds
Another common issue in the lifespan of molding systems is bearing failure. Linear guides and other moving parts in molding systems experience wear and tear like any mechanism. In roller bearings, the shape of the roller itself plays a key role in determining load distribution and, ultimately, the bearing’s lifetime.
Standard cylindrical rollers distribute the bearing loading evenly across the surface, with the exception of the edges. Along the edges the stress profile spikes dramatically, leading to localized wear and ultimately lowering the lifetime of the bearing. This design accelerates the degradation of both the roller and the bearing raceway, shortening the bearing’s operational life.
Redesigned roller profiles for more durable molds
To distribute the stress more evenly and reduce edge stress, rollers can instead be designed with a “crowned” profile. This shape change leads to a smoother, more uniform stress profile that allows the bearing to last longer.
It’s a small design adjustment that creates big improvements in bearing performance, especially in like automotive transmissions, heavy machinery, or power generation equipment. For molding applications, replacing simple linear guides with a specialized roller bearing system saves money in the long run.
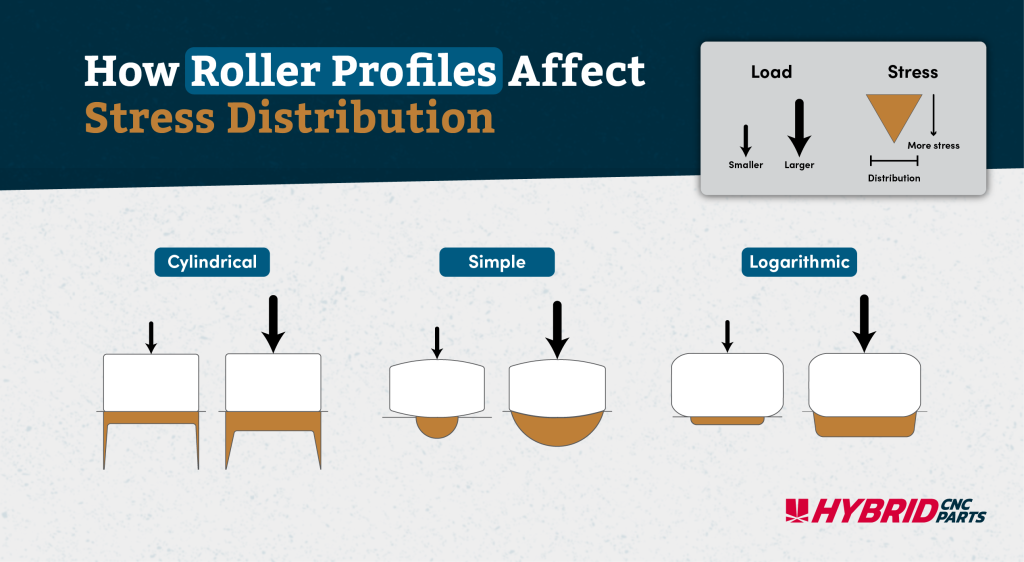
Image: Roller profiles and bearing loads affect the stress distribution along the roller. Sharp edges, even in chamfered rollers (e.g. cylindrical rollers) lead to spikes in the stress distribution, while more gently curved “crowns” (simple and logarithmic) lead to more uniform profiles and longer lifetimes. Schaeffler has extensive bearing design guides if you want to learn more. © Hybrid CNC Parts.
Using advanced materials for more durable mold bearings
Our friends, the superalloys, can be used alongside optimally-design roller profiles to extend bearing lifespans. For example, Inconel 718 has fantastic wear and creep resistance at high temperatures and would be a good choice for roller bearings in these situations.
By selecting the right roller profile and optimal material, manufacturers can ensure greater system reliability, lower maintenance costs, and a longer operational lifespan for their bearings.
Putting it together: Hybrid manufacturing for more durable molds
Creating custom pins and specialized roller profiles usually requires specialized equipment, and that comes at a cost, even if the long-term benefits outweigh the initial investment. This is where hybrid manufacturing–a type of advanced manufacturing that combines additive and subtractive manufacturing methods– provides the flexibility to create components in nearly any shape or size, with reduced costs for using high performance materials.
Wire-laser metal deposition (w-LMD) hybrid systems use lasers to melt wire feed stock, including many superalloys, into near net shape parts, which are then finished using traditional subtractive methods.
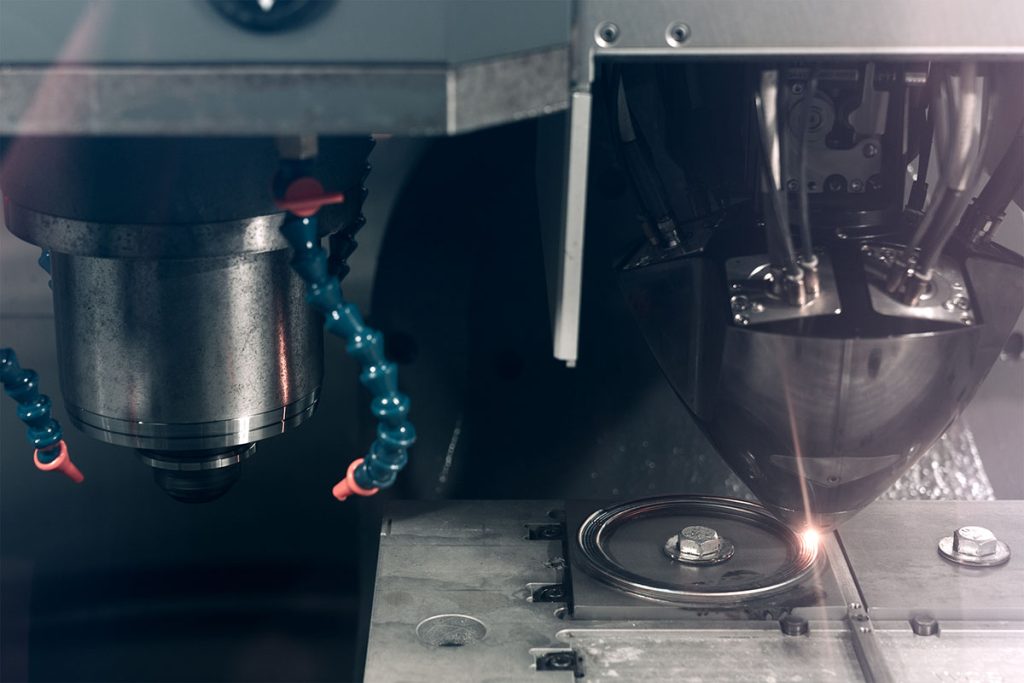
Image: One of Hybrid CNC Part’s Haas/Meltio systems at work. Here you can see additive wire-laser metal deposition being used to form a bearing component. To the left is the empty spindle of the CNC system that will later be used to refine the bearing shape with subtractive processes. © Hybrid CNC Parts.
By utilizing hybrid manufacturing techniques, custom-sized and -shaped pins and bushings can meet the specific needs of each mold, rather than relying on off-the-shelf solutions. This level of customization enhances operational efficiency, minimizes downtime, and leads to significant long-term cost savings.
But isn’t hybrid manufacturing/advanced materials expensive?
Additive manufacturing is often viewed as expensive and slow, but wire-laser metal deposition (w-LMD) offers a more efficient and cost-effective solution. Compared to powder-based metal additive manufacturing systems, w-LMD is faster, safer, and cheaper to operate. This makes it ideal for producing complex, high-performance components without the same overhead costs associated with other additive technologies.
In addition to production speed, w-LMD enhances return on investment (ROI) by reducing material waste and eliminating some post-processing steps. Superalloys and hardened tool steels become much more affordable when processed through w-LMD, as the technology builds components layer by layer from wire feed stock, minimizing material usage. More on these benefits below.
Reduced heat treatment costs
One of the key advantages of w-LMD hybrid manufacturing is its ability to heat treat components during the deposition process. With careful deposition control, the microstructure of the alloys can be hardened using the laser welding process. For example, H11 hot-work chromium tool steel parts can come off the build plate with a hardness of up to 58 HRC—a level typically achieved only after separate heat-treating steps. This ability to create hardened parts in situ not only speeds up production but also reduces costs associated with secondary heat treatments.
In cases where additional stress relief is necessary, components can still undergo annealing to eliminate residual stresses. However, the in situ hardening capability often means that fewer secondary processes are required, helping to streamline production and accelerate delivery timelines.
Less Material Waste Compared to Conventional Milling
In traditional manufacturing, significant amounts of raw material are lost during subtractive processes like milling or grinding, particularly when working with superalloys such as Inconel 718 or Stellite 6. These materials are expensive, and cutting them from solid stock creates substantial waste, increasing both material costs and machine time.
With w-LMD hybrid manufacturing, parts are built layer by layer from wire feed stock, which means only the material required for the part is used. This “near-net shape” fabrication minimizes waste, lowering material costs and improving sustainability. Additionally, because the parts come off the build plate with minimal excess material, less machining is required for finishing—reducing machine time and labor expenses.
This level of efficiency not only reduces the overall cost of using advanced materials but also makes it viable to use high-performance superalloys in applications where they were previously considered too expensive or excessive.
Wrap up: Molds and advanced manufacturing
Small though they are, mold components like pins and rollers play integral role in larger tooling systems. In industries like blow molding and injection molding, the repeated use of molds necessitates the constant replacement of parts to maintain product quality. Replacing molds or mold components takes time, money, and affects the bottom line.
Two ways to improve mold performance include choosing the right materials for the job and optimally-designed bearing rollers. Combined, these solutions can expand mold lifespans and increase overall production efficiency.
And by leveraging hybrid manufacturing, manufacturers can reduce lead times, minimize the need for post-processing, and achieve precision-engineered components that meet their exact specifications.
With advanced manufacturing, tailored solutions are a viable option for those manufacturers desiring longer-lasting components and extended mold lifespans.