Plastics processing encompass a wide range of high-temperature, high-wear applications—from injection molding of reinforced polymers to the extrusion of bioplastics for sustainable materials.
Plastics processors—like blow molders, injection molders, and extruders—rely on tooling for creating their products. These molds, dies, and related components need to function as optimally as possible, for as long as possible, to provide the best return on investment.
However, in the world of plastics, tooling is often subjected to some pretty demanding conditions which eventually contribute to failure. Operational environments with intense temperatures, erosive materials, and damaging off-gassing are common conditions plastic manufacturers face. Whether chemical, thermal, or mechanical in nature, the problems occurring due to corrosion and abrasion are fundamentally issues of durability.
Let’s Talk Durability
Durability, or a tool’s ability to maintain structural integrity and functionality over time, is critical to efficiency and profitability. Tooling durability affects not just product quality, but the costs associated with parts maintenance and replacement, production downtime, and overall equipment lifespan.
Even carefully chosen tool steels won’t last indefinitely, especially in more extreme operational conditions. The solution might appear to be to make tooling with more application-appropriate materials, like high-performance Inconel® or Hastelloy®. These superalloys offer great corrosion and wear resistance, but outfitting entire tooling systems with them would be prohibitively expensive for most manufacturers.
Other existing solutions center on surface treatments or coatings that extend tool life to a point. But for especially harsh environments—think the abrasiveness of glass-fiber-reinforced polymers or the corrosive by-products of certain plastics—a more targeted approach is needed.
Hybrid manufacturing is one such approach. By merging additive processes with subtractive machining, expensive alloys can be deposited only where they’re needed most, minimizing overall material costs while selectively boosting durability. We’ll get into more detail about how and why hybrid manufacturing is an ideal solution for corrosion and abrasion resistance later on in this post.
In this article, we’ll explore the fundamental corrosion and wear mechanisms that affect plastic tooling and discuss ways manufacturers can mitigate mold damage—covering everything from improved tool steels and coatings to strategic design changes. Finally, we’ll look at how hybrid manufacturing, along with other material and process innovations, offer a precise way to tackle corrosive and abrasive threats without breaking the bank.
Side note: While this article speaks about plastic manufacturing, the problems and solutions are equally applicable in glass and metal foundries.
Understanding Corrosion and Abrasion in Plastics Processing
Corrosion and abrasion present significant challenges in plastic processing, impacting equipment longevity, product quality, and operational efficiency. Various manufacturing methods—such as injection molding, extrusion, and blow molding—subject materials and machinery to extreme conditions, including high pressures, shear forces, and temperature fluctuations.
These factors, combined with the presence of abrasive fillers and corrosive additives, can lead to mold degradation, dimensional instability, and increased maintenance costs.
Understanding the interplay of these mechanisms is essential for optimizing production and extending the lifespan of tooling and machinery.
Injection Molding
Injection molding is characterized by rapid cycling, high-injection pressures, and localized shear at gates. Polymers can degrade under high shear or prolonged residence times, releasing corrosive compounds that attack mold surfaces.
In filled systems, the gate area experiences substantial abrasive wear as the polymer-fiber mixture jets into the cavity at high velocity. Over time, this combination of wear and chemical attack can degrade the mold surface, causing flash, dimensional drift, or surface defects.
Repeated heating and cooling cycles can accelerate corrosion, particularly in cooling channels where untreated water may deposit mineral scale or introduce corrosive contaminants.
Extrusion
In extrusion, the die and screw components face prolonged exposure to molten polymers under high shear and pressure.
In filled or reinforced systems, abrasive fillers such as glass or mineral fibers wear down die lips and flow channels, removing protective layers and exposing base metals to further corrosion. If the polymer contains acidic or halogenated additives, corrosion can take hold internally, leading to dimensional drift in the extrudate or even failure of the die itself.
If cooling systems within the die rely on untreated water, they are susceptible to scaling and corrosion, which can compromise heat transfer efficiency. This can lead to temperature inconsistencies, affecting product quality and causing increased wear in high-friction areas.
Blow Molding
Blow molding typically involves inflating a hot parison inside a mold, where cooling plays a critical role in cycle times and part consistency. Certain resins—especially halogenated or flame-retardant grades—can off-gas corrosive vapors that accumulate in vents, parting lines, or undercut areas, leading to pitting and crevice corrosion. These forms of corrosion may remain hidden until mold degradation starts affecting part quality.
A significant, yet often overlooked, source of corrosion in blow molding is the cooling system. Many blow molders use untreated water in cooling lines, leading to buildup of mineral scale and corrosion in internal cooling passages. Convoluted cooling channels with low flow rates can become stagnation points where localized corrosion accelerates, reducing thermal efficiency and increasing cycle times. Over time, this can result in reduced cooling performance, uneven part shrinkage, and premature mold failure.
Abrasive wear is another challenge, particularly in pinch-off areas, where excess plastic is compressed and severed during mold closure. This wear can be further exacerbated if reinforced or filled polymers are used, requiring frequent maintenance or tool replacement.
The Culprits: Corrosion and Abrasion
Common Corrosion Mechanisms in Material Processing
Let’s examine the following common means by which tooling suffers from corrosion damage: Uniform corrosion, pitting corrosion, galvanic corrosion, and stress corrosion cracking.
Uniform Corrosion
Uniform, or general, corrosion occurs when an unprotected metal surface is exposed to corrosive chemicals, causing a relatively even attack over the entire area.
While it might seem less dramatic than pitting or cracking, it steadily reduces cross-sectional thickness and can eventually compromise the tool’s mechanical integrity. In plastic molds, uniform corrosion often reveals itself as a dulling of polished surfaces or changes in cavity dimensions over time.
Causes of uniform corrosion in plastics processing include acidic off-gassing from halogenated polymers (like PVC), flame-retardant additives that decompose at high temperatures, and hydrolytic by-products in moisture-absorbing resins such as nylon or PET. If the mold material doesn’t have a certain threshold of corrosion resistance, or if the protective oxide film in steels (like 420 stainless) wears down, uniform attack can start to take hold.
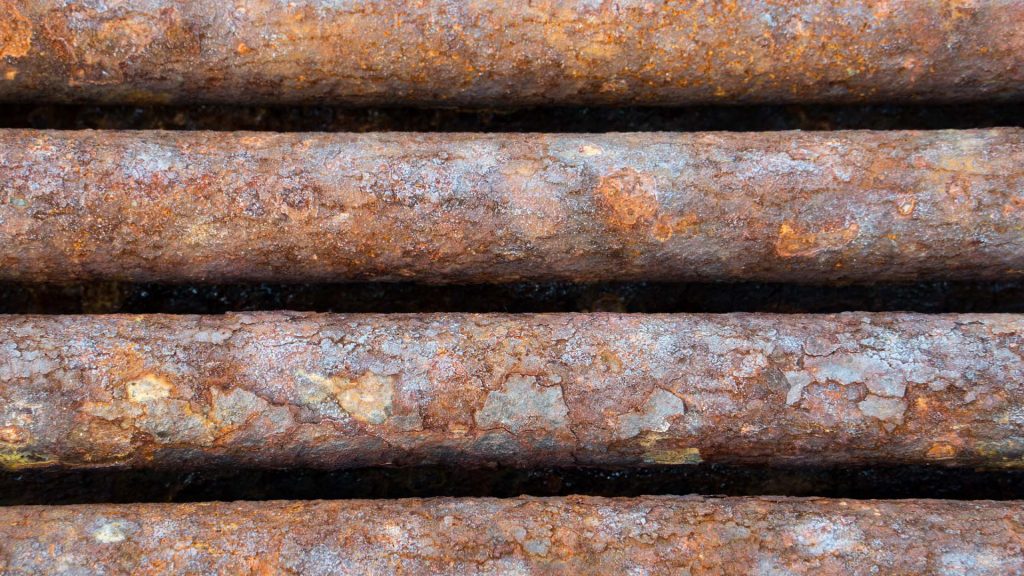
Figure 1: Completely rusted steel pipes showcase an example of uniform corrosion. Source: Adobe/judik.
Pitting Corrosion
Pitting corrosion is the formation of small, localized cavities or “pits” in the metal. These pits can be deceptively deep, even if the surface opening appears minor.
In the context of injection or blow molding, pitting is often catalyzed by chlorides or halogens in polymer feedstocks and can hide beneath surfaces until the tool’s performance noticeably suffers.
Pitting is particularly damaging because once it initiates, the geometry of the pit promotes an acidic micro-environment that perpetuates the problem.
Galvanic Corrosion
Molds rarely contain a single type of metal. You may have stainless steel inserts fitted into a hardened steel base, or different alloys used for core pins versus the cavity block.
If these dissimilar metals are in direct contact and there’s an electrolyte present—like water, or even humid air—electrochemical reactions can drive one of the metals to corrode preferentially.
In high-volume production environments, galvanic corrosion is especially relevant for cooling systems, where water can carry dissolved salts or impurities.
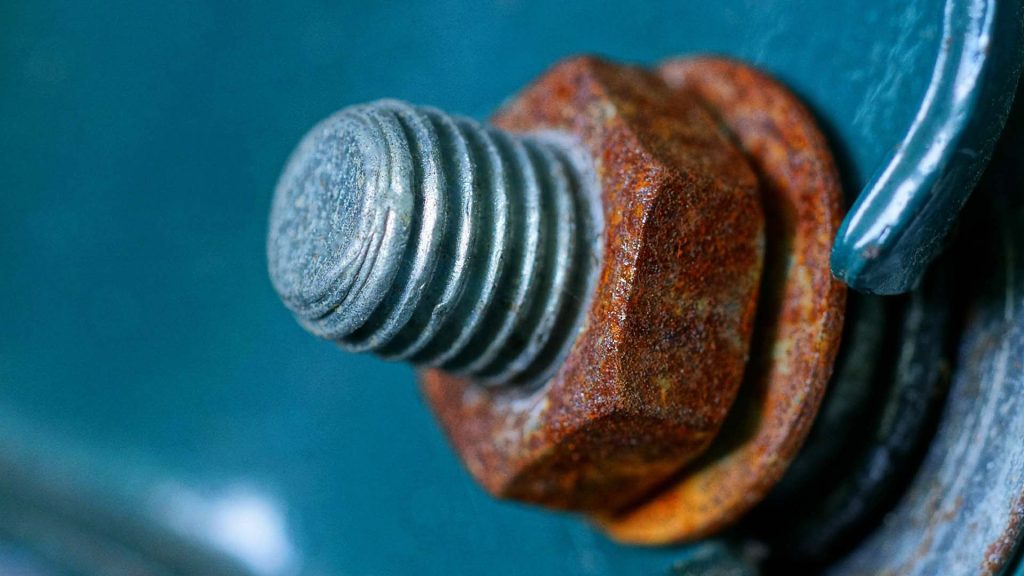
Figure 3: A rusted nut and non-rusted bold as an example of galvanic corrosion. Source: Adobe/butus.
Stress Corrosion Cracking
When you combine high-tensile stresses with a corrosive environment, you can end up with stress corrosion cracking (SCC), a brittle fracture mechanism that leads to sudden, catastrophic failures.
SCC can occur in materials that are subjected to certain chemical agents and mechanical loads simultaneously. In injection molding, regions around gates or ejector pin holes can experience high stresses; if the resin is also releasing halogenated or acidic by-products, SCC may strike without much warning.
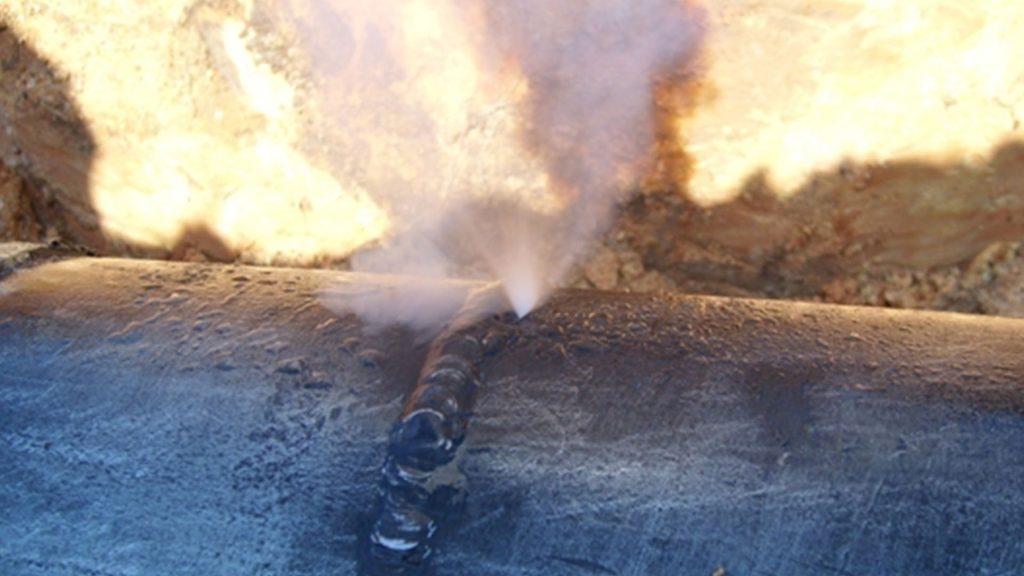
Figure 4: An example of stress cracking corrosion. Source: “Ammonia leak located close to a circumferential weld, at 12 technical hours from the pipeline.” by José Luis Mora-Mendoza, et al. is licensed under CC BY 4.0.
Abrasive Materials in Plastics Processing
Many molders contend with abrasion issues in addition to corrosion when processing fiber-filled or mineral-filled plastics.
Fiber-Reinforced Plastics
On top of corrosion, many molders also contend with abrasion when processing fiber-filled or mineral-filled plastics.
Glass-fiber–reinforced nylon, carbon-fiber–filled PEEK, and other high-performance blends are popular for their strength-to-weight ratio and improved mechanical properties.
However, these fibers scour the tool’s surface during injection or extrusion, wearing away protective coatings or oxide layers. Once the surface is compromised, even mild corrosives can rapidly attack the exposed base metal.
Mineral Fillers and Flame Retardants
Certain mineral fillers, like talc, mica, or calcium carbonate, can be abrasive as well—less damaging than glass fibers in many cases, but still able to erode sensitive features like gate edges, runner walls, and blow-mold pinch-off areas.
Flame retardants, depending on their chemistry, can contribute both to corrosion (via acidic decomposition by-products) and wear, if the additive is particulate in nature.
High-Temperature Molten Materials
High-temperature plastics, such as PEEK, PEI, and PPS, require processing temperatures that can exceed 572°F (300°C) in the mold cavity or extrusion die.
These elevated conditions accelerate both chemical reactions and mechanical wear. Any abrasive filler present in these resins is effectively rubbing against the mold at higher speeds and temperatures, compounding the erosive effect.
Solutions for Corrosion and Abrasion in Plastics Processing
Traditional Solutions
Traditional durability solutions rely on corrosion-resistant steels, high-performance alloys, and protective coatings to mitigate wear and chemical attack. While generally effective, these methods have limitations that can impact cost, manufacturability, and long-term performance. Let’s take a look at a few.
Corrosion-Resistant Steels
Stainless steels, such as 420 SS or 17-4 PH, and some higher-grade tool steels (like H13, when properly heat-treated) are commonly employed for molds that see corrosive conditions. These steels form a protective chromium oxide film, helping stave off general corrosion. However, even stainless steels can be susceptible to pitting or stress corrosion cracking if exposed to halides (chlorides, bromides) at high temperatures.
Nickel and Cobalt Alloys
For more extreme environments, such as highly acidic off-gassing or extremely high temperatures, nickel-based alloys (e.g. Inconel, Hastelloy) or cobalt-based alloys (e.g. Stellite®) offer superior corrosion and wear resistance. Yet their cost is significantly higher than typical tool steels, and machining them can be more challenging. Fully fabricating large tools with these materials is likely to be prohibitively expensive for most manufacturers.
Process Optimization
Coatings provide a barrier between the polymer melt and the underlying metal. Options include:
- PVD/CVD Coatings (e.g., TiN, CrN, TiAlN): Offer excellent hardness and moderate chemical resistance.
- Electroless Nickel Plating: Uniform coverage, including cooling channels and complex geometries. High-phosphorus coatings can improve corrosion resistance significantly.
- Nitriding or Nitrocarburizing: Creates a hardened surface layer on steel, with some degree of enhanced corrosion resistance depending on the process and base material.
Each coating has its strengths and limitations. A single coating may address either corrosion or wear effectively, but might need special topcoats or combined processes to handle both.
An Improved Approach: Optimizing Durability with Hybrid Manufacturing
While traditional approaches are valuable, they can be both expensive and limiting. That’s where hybrid manufacturing steps in.
Hybrid manufacturing integrates additive and subtractive processes. In general, it allows for more customization, material efficiency, faster production, and improved part performance.
This setup allows you to add layers of expensive, corrosion- and wear-resistant metal only in the areas that see the most severe conditions. Then, the same machine can mill or finish the part to the required tolerances.
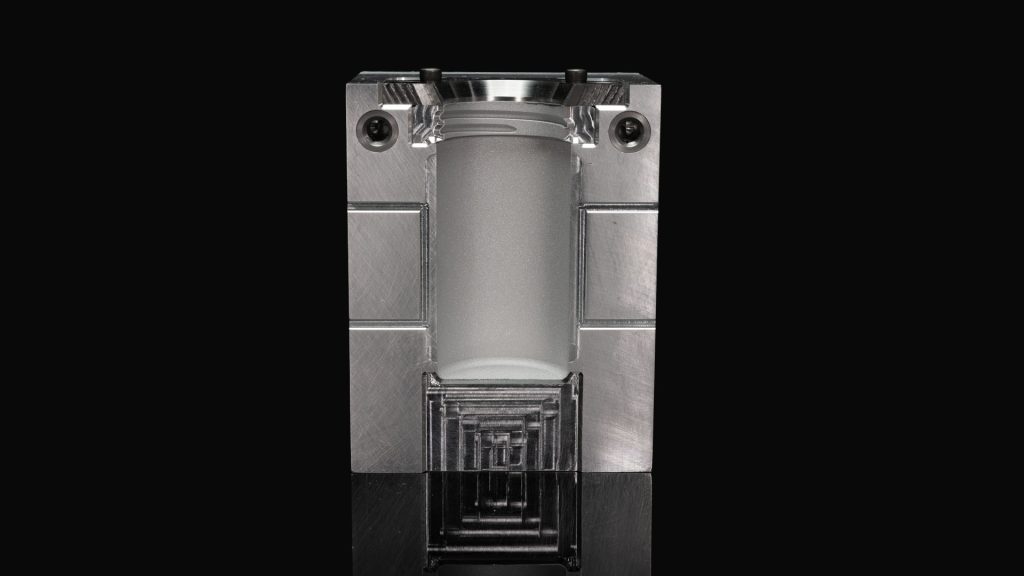
Figure 5: Half of a hybrid-manufactured mold. Copyright © Hybrid CNC Parts.
Types of Hybrid Manufacturing for Plastics Tooling
Knowing the different types of hybrid manufacturing is helpful in choosing the right method for your unique needs. There are several types of metal additive process that, when combined with CNC machining, provide hybrid manufacturing capabilities that can be used to create durable plastics tooling.
These processes can be divided into two categories based on the composition of the base material: wire or powder.
- Wire additive processes use metal wire as their feedstock, and include wire-laser metal deposition (w-LMD) and arc directed energy deposition (Arc-DED). While Arc-DED is best for large, high-deposition applications where speed matters more than precision, w-LMD is better for precision tooling and high-detail features.
- Powder additive processes use metal powder as their feedstock and include powder-bed fusion (PBF), binder jetting, and cold spray deposition. Each process has its own features and benefits, depending on the level of precision, mechanical strength, or resolution required.
While powder-based methods are capable of creating durable molds, they fall short when it comes to safety (the metal powder is highly flammable), material efficiency, and cost-effectiveness.
Wire-based methods, on the other hand, are relatively safe, fast, and more efficient when it comes to cost and materials.
Strategic Multi-Material Cladding to Mitigate Corrosion and Abrasion in Plastics Processing
Mold cavities or inserts that are subject to intense wear or corrosive off-gassing can be built up with more expensive, but higher performing, alloys (e.g. Inconel, Hastelloy, or Stellite) while the bulk of the mold block remains a less expensive steel ,like P20 or H13.
For extrusion dies, you might deposit a nickel-based alloy at the die lips where hot, abrasive plastic flow is most severe, while using tool steel in the upstream sections.
This multi-material approach drastically reduces raw material costs compared to machining an entire die from a solid superalloy block.
Extending Tool Life
Hybrid manufacturing also shines in repair and refurbishment. Let’s say the pinch-off area in a blow mold is eroded after millions of cycles. Instead of scrapping the entire mold or installing a new insert, you can remove the damaged region, deposit a fresh layer of wear-resistant metal onto the existing steel substrate, and machine it back to spec—all on the same machine. This technique saves time, reduces waste, and extends the tool’s life significantly.
By only using expensive alloys in limited areas, overall material costs drop dramatically. This strategic approach also aligns with sustainability efforts, as it reduces the mining and processing of high-alloy metals. Plus, the ability to refurbish critical regions effectively prolongs tool life, minimizing the scrap or disposal of larger tooling components.
Example Hybrid Use Case: Automotive Mold for High-Temp, Corrosive Material
Imagine a manufacturer tasked with producing large automotive parts using a flame-retardant, glass-filled nylon. This polymer runs at high temperatures, generating acidic off-gassing that attacks standard steels. The glass fibers abrade surfaces near the gate and in high-flow regions.
Traditionally, the mold for these parts might be made entirely from 420 SS or 17-4 PH, with some local insert upgrades. But the glass fiber still breaks down the surface, and the combination of acid-plus-abrasive media leads to frequent polishing and eventual replacements.
Economical Use of Superalloys
Using hybrid manufacturing, the main mold structure can be produced from a robust, yet economical, tool steel (like H13). Then, a 2-3 mm layer of Inconel, Stellite, or another superalloy can be added in the gating region and high-flow areas using a wire-based additive process.
After cooling, the same hybrid machine finishes the mold to achieve necessary geometry and surface profile. The cost is a fraction of machining an entire block of Inconel, yet the tool life in the critical areas is significantly extended. When wear does appear after many cycles, the damaged zones can be machined off and reclad with minimal downtime or waste.
Best Practice Processes
Even with a perfect hybrid-manufactured mold, best practices in process control remain vital. Drying hygroscopic resins, optimizing melt temperatures, and ensuring proper venting all help minimize the corrosive environment. Cooling line maintenance—ensuring water pH is in a safe range and free of chlorides—reduces the risk of galvanic or crevice corrosion inside channels. Monitoring part quality can reveal early signs of tooling wear or damage, prompting timely preventative maintenance rather than waiting for catastrophic failure.
Hybrid Manufacturing: An Efficient and Cost-Effective Solution
Addressing the challenges of corrosion and abrasion in plastics processing requires a multifaceted approach, with hybrid manufacturing emerging as a precise and cost-effective solution. While traditional methods such as corrosion-resistant steels and surface coatings offer some protection, they can be limiting and expensive, especially when dealing with extreme conditions.
Hybrid manufacturing, which integrates additive and subtractive processes, allows for the strategic use of high-performance alloys only in areas that experience the most wear and corrosion, significantly reducing material costs. This approach not only extends tool life but also aligns with sustainability efforts by minimizing the consumption of high-alloy metals and reducing waste.
Hybrid manufacturing offers benefits in repair and refurbishment, enabling the restoration of damaged tooling components by depositing fresh layers of wear-resistant metal. However, even with advanced techniques like hybrid manufacturing, adhering to best practices in process control is essential. These processes include drying resins, optimizing melt temperatures, ensuring proper venting, and maintaining cooling systems to minimize the corrosive environment and prevent premature tool failure.
By combining innovative manufacturing techniques with diligent process management, manufacturers can achieve enhanced durability, reduced downtime, and improved overall efficiency in their plastics processing operations.
Improve Your Tooling
We can help you achieve faster cycle times, superior part quality, and significant cost savings.
Contact us today to discuss your tooling needs.
Looking for more info?
Check out these other blog posts on hybrid manufacturing and tooling:
Contents
Contents