Remember the Space Race?
I sure don’t, but I have read a lot about it, and much of the technology developed during that time is still relevant today. After we landed on the moon in 1969, further space exploration was next on the list, and with that goal came its own set of challenges and resultant technological innovations that we can draw from today, more than five decades later. One of those areas of innovation was nuclear propulsion.
With the need to phase out fossil fuels and increased pressure on our national grid, nuclear energy will become a necessary component of future power generation plans. But it’s not without its own challenges—some of which can be resolved by looking backwards to the space race, but some will need a completely new approach involving innovative, modern manufacturing methods and materials.
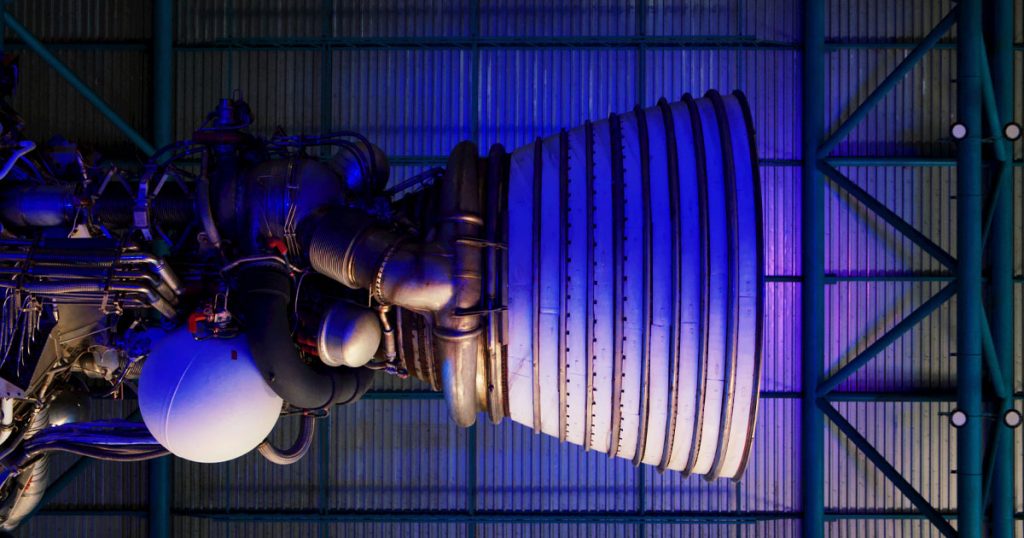
A Saturn V Rocket on display at the Kennedy Space Center. Unsplash / Brian McGowan.
In this post we’ll discuss some of the more relevant challenges involved in reviving space-age research to bring about next-generation nuclear energy today, and how advanced manufacturing methodologies can be used to make these updated nuclear facilities a reality.
Developing Nuclear Technology for Space Exploration
Let’s face it: engineering in space is no picnic. You can’t send a repair crew to fix something, and your parts are either frying or freezing, depending on whether the sun is in your way or not. Heat management in space is a counter-intuitive and punishing challenge—no air means no convection, which means precious few options for dumping waste heat.
Conventional power generation that works fine on earth—hydroelectric, batteries, fossil fuel combustion—don’t work as well in space. Chemical propulsion consumes fuel quickly, and to operate reliably and sustainably for years or decades, another solution is needed.
With a desire to explore beyond the moon, NASA was stuck with the question of how to power a spacecraft that needed to functionally operate in such extreme environments and for mind-boggling distances.
Enter nuclear power. With its high thrust-to-weight ratio and extended operational periods, nuclear offered an ideal energy source for space exploration. But there were still several challenges that needed to be overcome with the technology itself, including how to deal with scorching temperatures, relentless radiation, corrosive environments, and the need for long-lasting and robust systems.
Starting as early as the 1950s and intensifying with the monumental success of the Apollo 11 moon landing, NASA was willing and able to tackle these challenges. In 1961, NASA initiated its Nuclear Engine for Rocket Vehicle Application (NERVA) program, aimed at developing nuclear thermal rockets capable of interplanetary travel. By the late 1960s, NERVA had achieved several successful tests, demonstrating the feasibility of nuclear-powered space missions.
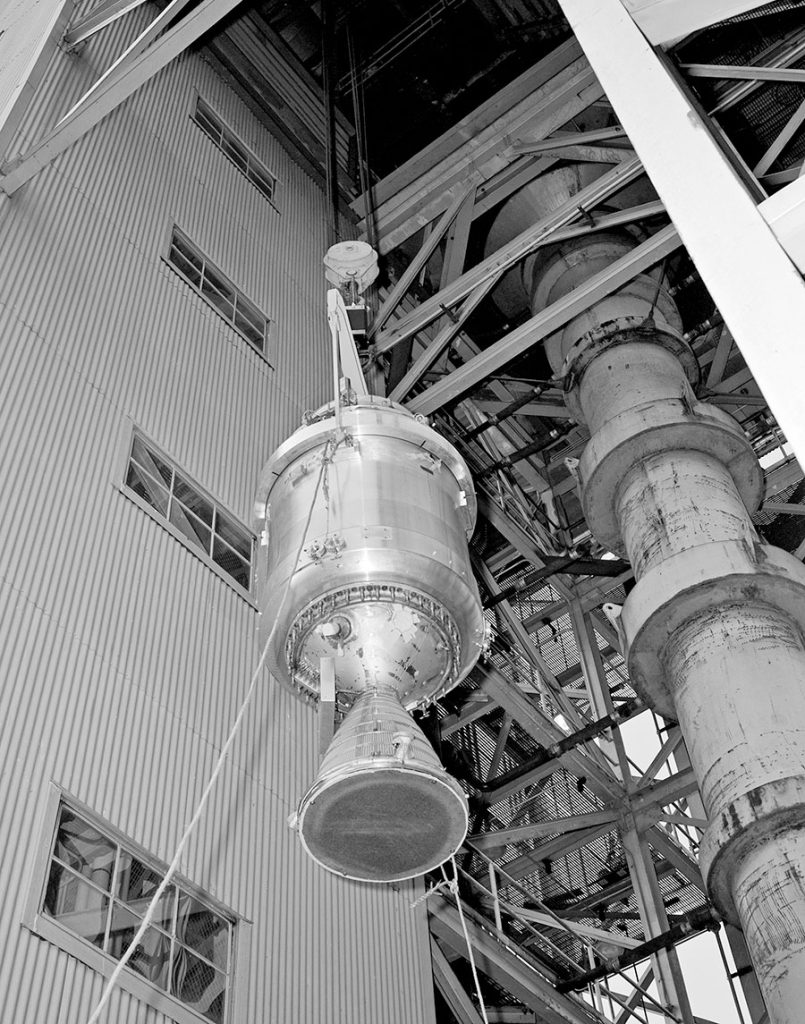
Installation of a Kiwi B–1B nuclear engine into the B-1 stand for testing of its propellant flow and startup systems (1963). NASA / Glenn Research Center.
However, as the Cold War intensified, national priorities shifted. The focus moved from space exploration to strengthening nuclear deterrence capabilities. This strategic pivot led to the redirection of nuclear resources from programs like NERVA to the development of nuclear weaponry and related defense technologies. Consequently, by the 1970s, NASA’s nuclear propulsion research was significantly scaled back and eventually discontinued.
Nuclear Energy: Then and Now
For better or worse, during the Cold War, the U.S. pivoted from exploring the peaceful potential of nuclear energy to focusing heavily on nuclear weapons.
Along with this shift came several high-profile disasters and near misses—like Chernobyl and Three Mile Island—which are probably what most people associate with the words “nuclear power”.
Regardless of our past uses and misuses, nuclear power remains an incredibly robust energy source that holds huge potential.
Today, with our national grid under increasing strain, it’s critical to push towards combining fossil fuels with renewable and sustainable energy sources—wind, hydro, geothermal, solar, and yes, nuclear. It has become a top priority for both the public and private sectors.
Next-Generation Nuclear Reactors
In recent years, the global energy landscape has undergone a dramatic shift. Reducing carbon emissions is no longer optional, and sustainable energy sources have become the cornerstone of efforts to combat climate change.
Amid this transformation, nuclear energy has re-emerged as a reliable, high-capacity option for meeting growing energy demands without compromising environmental goals.
Central to this revival are advanced reactor designs—specifically, Generation IV reactors —which offer significant improvements in safety, efficiency, and sustainability.
Generation IV Reactors
Generation IV reactors are designed to tackle the limitations of earlier models, such as waste management, accident prevention, and operational efficiency. They fall into four main categories:
- Sodium-Cooled Fast Reactors (SFRs): These reactors use liquid sodium as a coolant, allowing for high-temperature operation, which boosts efficiency. However, sodium’s high reactivity introduces safety and maintenance challenges, especially in the presence of water or air.
- Lead-Cooled Fast Reactors (LFRs): Utilizing liquid lead or lead-bismuth eutectic, LFRs benefit from excellent heat capacity and natural radiation shielding. These features make them robust and efficient, though lead’s density and potential for corrosion present unique material challenges.
- Molten Salt Reactors (MSRs): These reactors employ molten fluoride or chloride salts as both coolant and fuel medium. While MSRs excel in fuel efficiency and offer inherent safety features, the extreme corrosiveness of molten salts demands advanced, corrosion-resistant materials.
- Gas-Cooled Fast Reactors (GFRs): Helium is the primary coolant in GFRs, providing excellent heat transfer and avoiding the chemical reactivity concerns of liquid coolants. However, the low density of helium necessitates high-performance designs to optimize heat exchange and maintain efficiency.
Each of these reactor types comes with its own set of engineering hurdles. Corrosive environments, temperatures exceeding 1000°C, and intense radiation exposure push materials and mechanical systems to their limits.
Developing components for these systems isn’t just a matter of tweaking old designs—it requires a complete rethinking of materials, designs, and manufacturing techniques.
Making Mechanical Components for Nuclear Reactors
Nuclear reactors are intricate systems comprising numerous mechanical components that ensure their safe and efficient operation. Among these, moving parts such as bearings, impellers, and gears play pivotal roles.
Bearings
Bearings are fundamental in supporting rotating components, reducing friction, and ensuring smooth motion. In nuclear reactors, they are found in:
- Primary coolant pumps: These pumps circulate coolant through the reactor core, and their bearings must withstand high temperatures, radiation, and corrosive environments.
- Fuel handling mechanisms: To increase efficiency, there are some reactors designed with control rod drive mechanisms and in-vessel refueling machines that are in constant contact with high temperatures and potentially corrosive fluids. Bearings facilitate the precise movement of these mechanisms.
- Turbine generators: In reactors that generate electricity, bearings support the turbines connected to generators, requiring high reliability and durability.
Impellers
Impellers are rotating components designed to move fluids by converting rotational energy into fluid flow. In nuclear reactors, they are primarily used in:
- Coolant pumps: Impellers drive the movement of coolant, ensuring efficient heat transfer from the reactor core.
- Feedwater pumps: In pressurized water reactors, impellers in feedwater pumps are crucial for maintaining the flow of water into steam generators.
Gears
Gears are used to transmit torque and adjust rotational speeds between components. In nuclear reactors, they are found in:
- Control rod drive systems: Gears translate motor movements into the precise positioning of control rods.
- Auxiliary systems: Various support systems within the reactor utilize gears for operations such as valve control and instrumentation adjustments.
Challenges in Developing Mechanical Components for Generation IV Reactors
To fully understand the challenges involved in producing parts for modern reactors, we need to look at both the bigger-picture issues and the operating conditions.
The Supply Chain Puzzle
One of the biggest hurdles today is the supply chain. In the 1970s, a robust infrastructure supported the development of nuclear technologies. Specialty alloys, high-performance ceramics, and other advanced materials were widely available from a variety of suppliers who catered to the defense and energy sectors.
Fast forward to now, and that supply chain has significantly diminished. Many of the companies that once produced these niche materials have either pivoted to other industries or shut down entirely.
Globalization also complicates the picture. Sourcing critical materials now often means dealing with international suppliers, which introduces geopolitical risks, trade restrictions, and logistical challenges.
The recent focus on supply chain resilience—spurred by global events like the COVID-19 pandemic—has only underscored how vulnerable we’ve become to disruptions.
Manufacturing Capability
Even if you can get the right materials, who’s going to turn them into the parts we need? Manufacturing techniques have evolved dramatically since the 70s, but the expertise required to produce high-precision components for nuclear applications hasn’t kept pace in some areas. Specialized manufacturing facilities that once churned out components for space and defense are now few and far between.
And modern reactors demand parts that weren’t even on the radar back then. Advanced cooling systems, compact modular designs, and materials that can withstand decades of radiation exposure require cutting-edge manufacturing processes that simply didn’t exist before.
Missing Historical Knowledge
It’s true—we already cracked a lot of these challenges decades ago. Or at least we thought we did. The reality is more complicated.
Much of the knowledge from the 1970s exists, but it’s fragmented. Some of it is buried in archives, sitting in dusty filing cabinets, or even lost due to poor documentation. Other pieces are stuck behind layers of institutional knowledge, locked in the memories of retirees or in decommissioned programs that didn’t leave a clear paper trail.
Picking up where we left off means embarking on a sort of technological treasure hunt. But even if we find the blueprints and technical reports, that’s only half the battle. The world has changed in significant ways since those early days of nuclear research.
Generation IV reactors introduce new designs and operational conditions, presenting unique challenges for the mechanical components they contain.
Operating Conditions
Generation IV reactors introduce new designs and operational conditions, presenting unique challenges for mechanical components, including:
- High-temperature operation: Some designs can reach temperatures exceeding 1000°C, necessitating materials and bearings that can maintain integrity under such conditions.
- Corrosive coolants: Reactors using molten salts or liquid metals as coolants require components resistant to corrosion and erosion. MSRs utilizes molten fluoride salts, which are highly corrosive and can react poorly with particular alloying elements.
- Radiation exposure: All components within the reactor environment are subjected to intense radiation, leading to material degradation. Developing radiation-resistant materials is crucial for the longevity of bearings and other moving parts.
- Maintenance and accessibility: Designs that minimize the need for maintenance or allow for remote handling are essential, given the hazardous environment. This consideration impacts the design and selection of mechanical components.
Solving Today’s Nuclear Challenges
The good news? We’ve made incredible strides in materials science, computational modeling, and manufacturing since those early days at NASA.
High-performance materials, like superalloys, are ideal for creating components that will survive the harsh conditions found in Gen IV reactors.
Advanced simulation tools using non-equilibrium thermodynamics, finite element analysis, and data-driven sensing and monitoring let us test designs virtually under conditions that would be impossible or prohibitively expensive to replicate physically, reducing development cycles and enables rapid iteration.
And advanced manufacturing techniques allow us to create components that are not only stronger and lighter, but also more cost-effective.
Combining Past Lessons with Advanced Manufacturing
By integrating advanced materials and manufacturing with lessons from past nuclear programs, we can produce components that meet the rigorous demands of this latest generation of reactors while laying the foundation for a more sustainable and resilient energy future.
Hybrid manufacturing, an advanced manufacturing method that combines additive and subtractive processes, is ideal for producing the precise, robust, and complex geometries required for these parts.
Specifically, hybrid wire-laser metal deposition (w-LMD) is the optimal choice when it comes to hybrid production for nuclear. Using lasers to melt wire feedstock, it produces sophisticated, fully-dense parts which are fine tuned using traditional subtractive methods. w-LMD units are typically integrated within modern CNC machines that offer advanced features, like 5-axis control.
Hybrid w-LMD Solutions
Generation IV systems have been designed to be cleaner, safer, and more efficient than previous generations of nuclear reactors. But their innovative features require innovative manufacturing—that’s where hybrid w-LMD comes in. Below are some of the areas hybrid w-LMD can solve the challenges facing Gen IV component production.
Cooling and corrosion
To combat the excessively high temperatures and corrosive environments within Gen IV nuclear systems, features such as intricate internal cooling channels can be 3D printed using superalloys like Inconel® or Hastelloy®. Components that could benefit include everything from bearings to gears.
Structural integrity
Parts hybrid manufactured with wire-laser metal deposition are fully dense, and this fabrication method allows the integration of custom or complex design features that contribute to component integrity and performance under extreme conditions For example, impellers can be manufactured with complex geometries that optimized flow paths and efficiency.
Targeted functionality
Hybrid w-LMD manufacturing can also be used to enhance the functionality of existing components by layering dissimilar materials or cladding high-performance alloys on top of standard materials. This technique allows engineers to target critical zones of a component—such as bearing contact surfaces or impeller blade tips—with high-performance materials.
By applying superalloys or corrosion-resistant coatings only where they’re needed, we can significantly improve wear resistance, thermal stability, and corrosion protection while minimizing material waste.
For example, in a coolant pump impeller, hybrid w-LMD can be used to reinforce the leading edges of the blades, which experience the highest wear from fluid flow.
Similarly, for gears in control rod drive systems, this method can strengthen high-stress teeth surfaces without altering the bulk material properties of the gear body. This targeted approach not only enhances performance but also reduces overall manufacturing costs and component weight.
De-risking Supply chains
Traditional manufacturing of advanced alloy components faces significant hurdles, including small production volumes, high material costs, and limited manufacturing pipelines. Hybrid manufacturing solves many of these issues by utilizing a single feedstock—welding wire of the required alloy—to create a variety of component geometries and form factors.
This adaptability simplifies the supply chain, reduces dependency on specialized suppliers, and accelerates production timelines.
The Future of Innovation in Nuclear Tech
The journey of nuclear technology, from the ambitious space propulsion projects of the 1960s to today’s cutting-edge reactor designs, highlights the critical importance of reliable and robust mechanical components in ensuring reactor safety and efficiency.
As we confront today’s challenges to energy security and environmental sustainability, the need to revive and build upon historical research becomes ever more pressing.
Engineers and researchers must delve into the archives of past studies, conducting “information archaeology” to uncover valuable insights. Combined with the advances in methods and materials that advanced manufacturing offers, we can create the next generation of bearings, impellers, and gears that will make the newest generation of nuclear reactors a reality.
Discover Hybrid Manufacturing
Learn more about the capabilities of hybrid w-LMD manufacturing.