What is Conformal Cooling?
Conformal cooling represents a cutting-edge approach to thermal management in manufacturing processes, particularly in injection molding, blow molding, and die casting.
Cooling channels are integrated into the mold itself and internally follow the contours of the cavity. Working with the geometry of the tool achieves a level of precision and efficiency that traditional straight-line cooling channels can’t match.
The fundamental goal of conformal cooling is to address longstanding issues with uneven heat dissipation, which can lead to defects such as warping, residual stress, and inconsistent part quality.
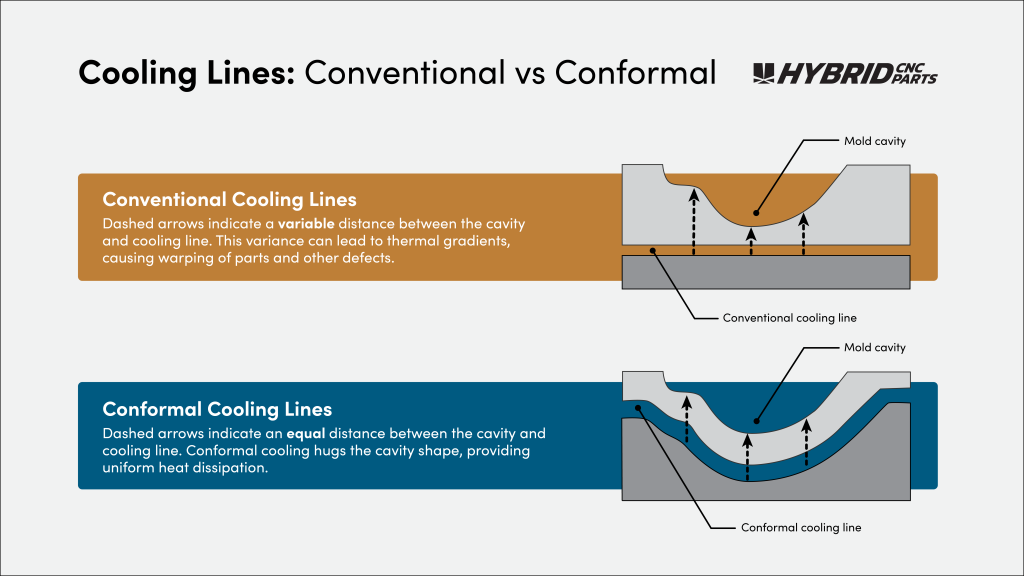
Conventional versus conformal cooling lines. Conventional cooling lines are linear, with variable distances between the mold cavity and the cooling line—resulting in thermal gradients. With conformal cooling, the cooling lines are equidistant from the cavity and provide a more uniform heat dissipation. © Hybrid CNC Parts.
By running internal cooling channels that conform to a cavity’s shape, and by always keeping those channels equally distant from the cavity, it becomes possible to remove heat more uniformly. More even head dissipation can cut down on cycle times and improve product quality—all while reducing energy costs.
This innovation is powered by advanced manufacturing technologies such as additive manufacturing, hybrid processes, and computational design tools, making conformal cooling a hallmark of modern engineering and production.
However, its adoption has been gradual due to challenges related to cost, expertise, and integration into existing workflows.
In this post we’ll explore the types of conformal cooling available today, the materials and manufacturing methods that make it possible, its challenges, and the potential it holds for transforming industries like automotive, aerospace, medical devices, and consumer goods.
Conformal Cooling Designs for Molds
There are multiple ways to design conformal cooling, each achieving varying degrees of thermal efficiency.
Let’s explore three designs for a theoretical injection molded cup. In each example, the transparent core is the boss on which our cup will be molded and the conformal cooling design is shown in blue.
We’ve also assigned a completely arbitrary Cooling Efficiency Rating for each.
Conformal Cooling Design 1: Spiral
With the spiral design, we can see the cooling line coiled inside the otherwise solid part. This design satisfies our conformal cooling metric by always keeping the lines equidistant from the cavity surface.
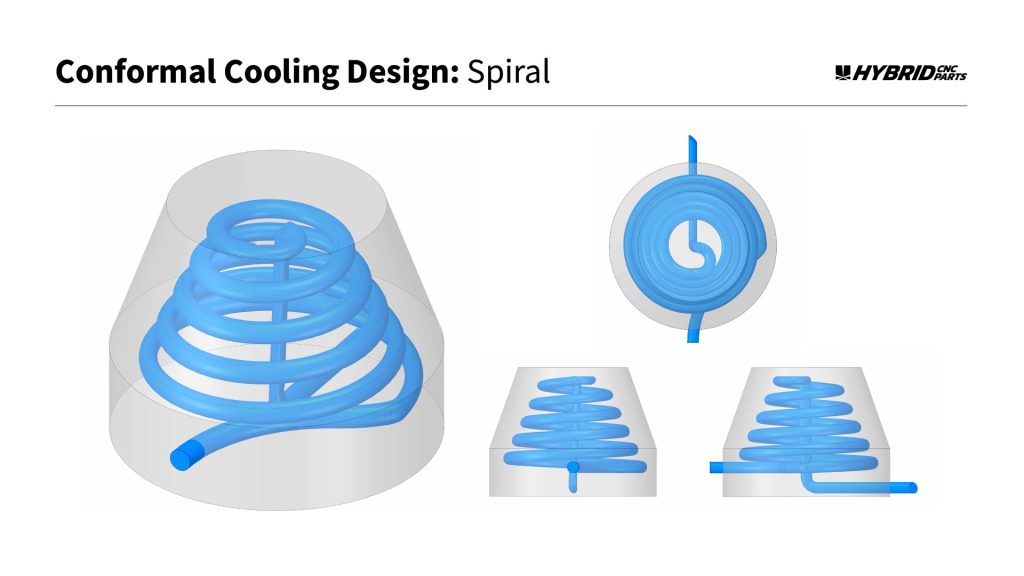
Figure: Example of a conformal cooling for molds “spiral” design. © Hybrid CNC Parts.
Unfortunately, even though this geometry hugs the surface tightly, the long distance that the channel travels is inefficient, and would potentially lead to substandard cooling performance.
Cooling Efficiency Rating: 1/5
Conformal Cooling Design 2: Cage
This design resembles a birdcage, with cooling fluid deposited in a disc-shaped distribution channel near the top before sending the fluid down parallel channels that collect in a ring shape and then released.
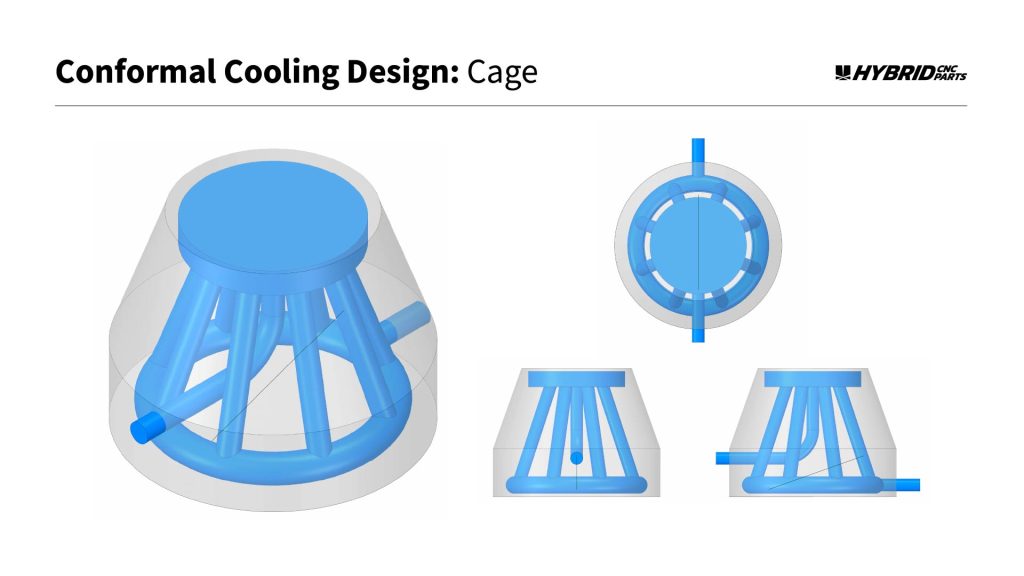
Figure: Example of a conformal cooling for molds “cage” design. © Hybrid CNC Parts.
This is a more efficient design due to the shorter distances the coolant needs to travel, and would also be easier to manufacture since there are fewer extreme overhangs.
Cooling Efficiency Rating: 3/5
Conformal Cooling Design 3: Insert
What’s different about this third design is that it consists of an cooling insert (which contains cooling channels) and the insert and boss are mated together.
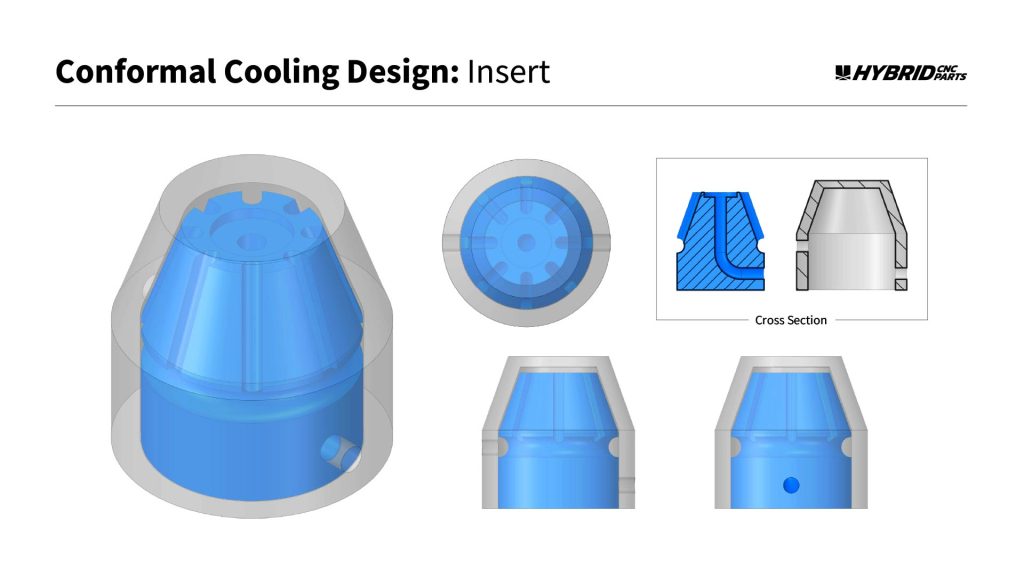
Figure: Example of a conformal cooling for molds “inset” design. © Hybrid CNC Parts.
Inside the insert are cooling elements that require additive manufacturing to achieve, while the distribution disc and return channels are subtractively manufactured into the surface of the insert.
By combining additive and subtractive manufacturing methods with a hybrid process, this design allows for the the geometric complexity that achieves the thermal transport efficiency required while also taking advantage of the relatively quick/easy/cheap subtractive manufacturing operations performed on the exterior surface.
This kind of lateral design thinking can integrate what appears to be an expensive or niche application into commercial injection or blow molding.
Cooling Efficiency Rating: 5/5
Optimal Materials for Molds with Conformal Cooling
Selecting the right material for conformal cooling molds is critical. The ideal material must balance thermal conductivity, mechanical strength, and machinability, while also withstanding operational stresses like high temperatures and injection pressures.
Tool Steels
Examples: H13, P20
Why They’re Used
Tool steels are highly durable and heat-resistant, making them ideal for molds subjected to high pressures and temperatures. They are particularly effective for long production runs, where wear resistance is crucial.
Limitations
Lower thermal conductivity compared to materials like copper alloys results in slower heat dissipation. This issue often necessitates additional cooling strategies or inserts.
Copper Alloys
Examples: Beryllium Copper (C17200), Copper-Chromium-Zirconium CuCrZr
Why They’re Used
Copper alloys excel in thermal conductivity, ensuring rapid heat dissipation. This property helps minimize cooling times, which is especially valuable in high-speed production environments like bottle cap or automotive part molding.
Limitations
Copper alloys are softer and less wear-resistant than tool steels. As a result, they are often used as inserts or localized features within molds rather than for the entire mold structure.
Maraging Steels
Examples: Maraging 300 (1.2709)
Why They’re Used
Maraging steels are highly compatible with additive manufacturing processes. Their high strength and ease of heat treatment make them ideal for 3D-printed molds, particularly those incorporating conformal cooling channels.
Limitations
They are more expensive than traditional steels and have lower thermal conductivity than copper alloys, making them less efficient for applications where heat transfer is a priority.
Nickel-Based Alloys
Examples: Inconel® 718
Why They’re Used
Known for their exceptional thermal fatigue resistance and mechanical strength, nickel-based alloys are suitable for molds operating under extreme conditions, such as high-stress injection molding or die casting.
Limitations
These alloys are costly and difficult to machine, requiring advanced equipment and expertise. Their use is often limited to highly demanding applications.
Multiple Alloys
Examples: Copper+H13, Maraging 300+Inconel 718
To achieve optimal performance, conformal cooling molds can use composite materials or hybrid designs that combine the strengths of different materials.
For instance:
- A mold core might use copper inserts for efficient heat transfer, while the surrounding structure is made from H13 steel for durability.
- Additive-manufactured components may integrate maraging steels for complex channels while employing nickel-based inserts in high-wear areas.
This multi-alloy approach ensures that the mold balances performance, durability, and cost efficiency.
The Current Conformal Cooling Landscape
The conformal cooling market is primarily driven by advanced manufacturing technologies, such as additive manufacturing and hybrid processes.
Below are the currently available options if you want a mold with conformal cooling, including their respective strengths and weaknesses.
Additive-Manufactured Molds
These molds are made using metal 3D printing methods like laser powder bed fusion (LPBF) or directed energy deposition (DED). These methods allow for the creation of intricate conformal channels.
Strengths
Ideal for highly complex geometries, such as molds for medical devices or automotive trim panels.
Weaknesses
Limited by build volume and the speed of additive manufacturing. Requires additional post processing.
Hybrid-Manufactured Molds
Hybrid molds combine additive techniques with subtractive CNC machining. Conformal channels are 3D printed and then critical surfaces are milled for precision, all within the same system.
Strengths
Balances the flexibility of additive manufacturing with the precision of traditional machining. Saves time by integrating processes within the same system.
Weaknesses
Requires significant design and manufacturing expertise to integrate both processes. Equipment costs can be prohibitive.
Off-the-Shelf Conformal Cooling Inserts
Some companies, like HASCO and DME, offer standardized conformal cooling inserts that can be integrated into traditional molds.
Strengths
Cost-effective for common applications.
Weaknesses
Limited customization; not ideal for highly specific geometries.
High-Conductivity Inserts
For molds where additive manufacturing is impractical, inserts made from high-conductivity materials like beryllium copper or thermal graphite are used to approximate the benefits of conformal cooling.
Strengths
Well-suited for molds with simple geometries.
Weaknesses
Lacks the flexibility of fully-custom conformal cooling designs.
Challenges with Conformal Cooling for Molds
Despite its undeniable advantages, conformal cooling has struggled to achieve widespread adoption across industries. Below are the key reasons hindering its uptake.
High Initial Costs
The upfront cost of creating a conformal cooling mold is significantly higher compared to traditional molds, largely due to the reliance on advanced manufacturing technologies such as additive manufacturing and hybrid techniques. These methods require:
- Expensive Equipment: Metal 3D printers and hybrid systems involve substantial capital investment.
- Specialized Materials: Maraging steels, copper alloys, and nickel-based alloys used for conformal cooling can be costly.
- Post-Processing Needs: Additive processes often require additional steps like surface finishing or heat treatment, further increasing costs.
For small and medium-sized businesses, these upfront expenses can be prohibitive, especially when the return on investment is not immediately apparent.
Lack of Expertise
Designing and implementing conformal cooling solutions demands a high level of technical expertise, which many companies lack. Specific challenges include:
- Advanced CAD Skills: Engineers must design intricate cooling channels that conform to complex geometries while ensuring manufacturability.
- Additive Manufacturing Knowledge: Understanding the nuances of metal 3D printing, including build orientation, support structures, and material behavior, is critical.
- Thermal and Fluid Simulations: Proficiency in tools like ANSYS Fluent or Autodesk Moldflow is necessary to optimize cooling performance and predict thermal behavior.
The steep learning curve and limited access to trained professionals make it difficult for many manufacturers to adopt conformal cooling without external support.
Compatibility Issues
Integrating conformal cooling into existing production systems presents several challenges:
- Coolant Optimization: Cooling channels need to be designed for specific coolants (e.g., water, oil, or air) to ensure efficient heat transfer without causing turbulence or pressure loss.
- Material Constraints: The mold material must not only offer thermal conductivity but also withstand operational stresses like high injection pressures and abrasive wear.
- System Integration: Conformal cooling molds may require modifications to existing cooling infrastructure, such as pumps, fittings, and controllers, which adds complexity.
Risk Aversion
Transitioning from proven methods to new, less familiar technologies like conformal cooling feels like a gamble due to:
- Uncertainty About ROI: Companies may question whether the long-term savings in cycle time and energy costs justify the initial investment.
- Fear of Failure: A poorly designed conformal cooling mold could lead to defects, downtime, or higher maintenance costs, which can be catastrophic in production-critical industries.
- Conservative Culture: Many industries prefer to stick to “what works,” even if it is less efficient, rather than experimenting with novel technologies.
Benefits of Conformal Cooling for Molds
While the adoption of conformal cooling has been slowed by challenges such as high costs, expertise requirements, and integration difficulties, its advantages offer transformative potential for manufacturing. These benefits include:
Increased Efficiency and Productivity
Conformal cooling reduces the time required for molds to cool between production cycles, directly accelerating cycle times. Traditional cooling channels often fail to address uneven heat dissipation, which prolongs cooling phases.
By conforming to the cavity geometry, these advanced cooling designs:
- Maximize heat transfer efficiency.
- Enable manufacturers to produce more parts in less time.
- Improve overall throughput and operational efficiency.
Enhanced Part Quality
Uneven cooling in molds leads to defects such as warping, residual stress, and inconsistent dimensions. Conformal cooling eliminates these issues by maintaining uniform temperature distribution across the entire mold surface.
The result is better overall part quality and reliability, including:
- Better surface finishes.
- Tighter tolerances.
- Reduced rejection rates.
Energy Savings
Conformal cooling designs allow for quicker and more effective heat removal, reducing the energy required to maintain the cooling process. The minimized cooling phase not only shortens production cycles but also lowers the operational load on cooling systems like pumps and chillers.
This energy efficiency translates into:
- Significant cost savings over the lifecycle of the mold.
- Improved environmentally sustainable processes.
Extended Mold Lifespan
Localized heat accumulation in traditional molds often leads to thermal stress, which can weaken materials over time and lead to cracking or deformation. Conformal cooling prevents such issues by ensuring even heat distribution, thus minimizing stress concentrations.
Conformal cooling extends a mold lifespan through:
- Prolonged operational life.
- Reduced maintenance needs.
- Delayed costly mold replacements.
Long-Term Cost Savings
Although conformal cooling molds often have higher upfront costs due to specialized manufacturing techniques and materials, their efficiency results in significant long-term savings. Over time, the benefits outweigh the initial costs, providing a compelling return on investment.
Initial investment is recovered through:
- Faster cycle times.
- Reduced energy consumption.
- Lower scrap rates.
Improved Process Consistency
Inconsistent cooling in traditional molds can lead to variability in part dimensions, material properties, and overall quality. Conformal cooling ensures a consistent thermal environment, allowing for repeatable, predictable outcomes across production runs.
This consistency:
- Minimizes downtime due to defects or adjustments.
- Improves overall process reliability.
- Improves production schedules.
Advanced Design Capabilities
Traditional cooling methods limit mold designs due to the linear nature of conventional channels. Conformal cooling, enabled by additive manufacturing and hybrid techniques, allows channels to follow the contours of complex geometries.
- Customization for Complex Geometries: Conformal cooling channels can be designed to match intricate shapes, including those with sharp angles, curved surfaces, or irregular contours. This capability is especially useful for industries like automotive, aerospace, and medical devices, where parts often feature complex designs that demand precision.
- Additive Manufacturing Integration: Additive manufacturing allows for the creation of overhangs, twists, and turns in cooling pathways that would be impossible to achieve with conventional subtractive methods.
- Improved Cooling for Small or Thin Features: Conformal cooling can be applied to molds for parts with thin walls, narrow ribs, or other delicate features. Traditional cooling methods struggle to efficiently manage heat in these areas, but conformal cooling can target and evenly dissipate heat in small, critical zones, preserving part quality.
- Greater Design Freedom: By removing the constraints imposed by straight-line cooling channels, designers have more freedom to innovate. This flexibility supports the creation of molds for lightweight, high-performance parts with intricate internal structures, such as lattice patterns, honeycomb cores, or aerodynamic shapes.
- Integration of Multi-Functional Features: Conformal cooling enables the integration of additional functionality into the mold, such as combining cooling with venting or structural reinforcement. This ability can reduce the number of manufacturing steps and improve overall efficiency.
Despite the initial hurdles, the long-term advantages of conformal cooling make it a worthwhile investment for manufacturers seeking to improve efficiency, product quality, and competitiveness.
Conclusion
Conformal cooling represents a transformative innovation in thermal management for manufacturing processes, offering substantial benefits in cycle time reduction, product quality improvement, and energy efficiency.
By leveraging advanced manufacturing technologies like additive and hybrid processes, this approach pushes the boundaries of mold design, making it a powerful tool for industries striving for precision and efficiency.
However, widespread adoption remains a challenge due to high initial costs, technical expertise requirements, and integration complexities. Overcoming these hurdles will require continued advancements in materials, manufacturing methods, and industry education.
As these barriers are addressed, conformal cooling has the potential to become a standard in modern manufacturing, driving significant gains in productivity and sustainability across diverse industries.
Ready to Upgrade Your Molds?
With our expertise in optimizing thermal performance, material selection, and manufacturing integration, we can help you achieve faster cycle times, superior part quality, and significant cost savings.
Contact us today to discuss your conformal cooling needs.
Looking for more info?
Check out these other blog posts on hybrid manufacturing and molds:
- Overcome Conventional Moldmaking Limitations with Hybrid Manufacturing (8 min read)
- More Durable Molds that Last Longer with Advanced Manufacturing (10 min read)
- How to Improve ROI with Hybrid Manufacturing (14 min read)
And if you want to dig deeper into injection mold design, David Kazmer’s Injection Mold Design Engineering (2007) is an excellent choice.