Bearings are vital to the functioning of countless machines, from skateboards to satellites. They can be a small part of a big system, and so their importance often goes unnoticed, especially when they function seamlessly under ordinary conditions.
However, when placed in challenging environments, the demands on bearings escalate dramatically. Corrosive geothermal brine while drilling deep wells. High-temperature operations inside a nuclear reactor. Punishing radiation and massive temperature swings on orbiting spacecraft. All of these applications require bearings, and all these environments would devastate regular ones.
In these extreme environments, bearings must be engineered to withstand conditions that push materials and designs to their absolute limits.
What We’ll Discuss
In this article, we explore the critical role bearings play in extreme environments and the unique challenges these settings present. We’ll delve into the advanced manufacturing methods we use to produce these robust components and discuss the rigorous testing that ensures their reliability.
Finally, we’ll demonstrate why Hybrid CNC Parts is at the forefront of this field, offering solutions that are a true game-changer for industries operating in the harshest environments on Earth—and beyond.
Understanding Bearings and Extreme Environments
Over 4,000 years ago, a group of Neolithic people accomplished a monumental feat: constructing the awe-inspiring Stonehenge. Among the numerous theories surrounding this ancient marvel, one suggests that wooden bearings played a crucial role in transporting the massive stones across Salisbury Plain.
Fast forward thousands of years to Leonardo da Vinci, the renowned polymath, artist, and engineer, who sketched the first documented aerospace design. Da Vinci’s intricate ball bearing designs would later become integral components in various machines.

A sketch by Leonardo da Vinci in the Codex Madrid c.1500 depicting an early ball bearing design for da Vinci’s helicopter.
These two seemingly unrelated examples share a fundamental principle: the need to reduce friction and wear. Dealing with friction between two surfaces is an age-old engineering challenge, and it lies at the heart of the fascinating field of tribology, which investigates friction, wear, and lubrication. Tribology underpins the inner workings of countless everyday items and industries, with bearing performance ultimately created through the complex interaction between fluid dynamics and material science.
A full discussion of tribology would be an entire series on its own, so let’s stay focused on bearings in extreme environments. At its core, a bearing’s primary function is to reduce friction between two surfaces in relative motion, thereby allowing the smooth and efficient operation of machinery. Bearings come in various forms, including ball bearings, roller bearings, and thrust bearings, each designed to handle different types of loads and motion. While the basic principles of operation remain consistent, the materials and bearing designs must be tailored to their specific applications, especially in extreme environments where standard solutions are inadequate.
Why Bearings Perform Poorly in Extreme Environments
Extreme environments place extraordinary demands on bearings. The combination of high temperatures, corrosive chemicals, high pressures, and poor lubrication can severely degrade the performance of standard bearing materials, leading to premature wear and failure.
To understand why they fail, we need to understand the factors that influence bearing performance in challenging conditions.
Poor lubrication environments
In many extreme environments, particularly in space, nuclear, or deep-sea applications, traditional lubricants are ineffective. The vacuum of space causes most lubricants to evaporate, while deep-sea conditions may lead to their breakdown or washout. In nuclear systems, a combination of chemical compatibility and high temperatures renders most traditional lubricants ineffective.
Without adequate lubrication, metal surfaces within the bearing come into direct contact with one another, leading to increased friction, wear, and ultimately, failure. This situation is exacerbated by the lack of elastohydrodynamic lift, which normally helps to separate moving surfaces and reduce wear.
High operating temperatures
Bearings used in applications such as geothermal drilling or nuclear reactors must withstand extremely high temperatures. At these elevated temperatures, traditional bearing steels, like 52100, can lose their hardness, leading to accelerated wear and reduced fatigue life. Because the microstructure of the steel changes at high temperatures, it causes a reduction in its mechanical properties.
Other common bearing materials may suffer from creep, oxidation, or other temperature-induced degradation, making them unsuitable for such environments.
Corrosive environments
Geothermal wells, nuclear reactors, and certain aerospace applications expose bearings to highly corrosive environments. In geothermal wells, the presence of hot, acidic water can lead to the rapid corrosion of standard bearing materials. Similarly, in nuclear reactors, the combination of high radiation levels and corrosive coolants, such as sodium, molten salt, or liquid lead, requires the use of materials that can resist both corrosion and radiation damage. These conditions often necessitate the use of specialty alloys or coatings that can withstand these harsh conditions.
Supply chain limitations
Most bearings are manufactured using highly optimized processes designed for mass production. The capital expenditure required to fabricate bearings with new designs and specialty alloys is usually cost-prohibitive, especially when high-performance applications call for low-volume production runs.
This situation leads to supply chain challenges, as finding small quantities of high-performance parts can be difficult when most manufacturers require large minimums and rely on conventional production methods.
Manufacturing Bearings for Extreme Environments
The manufacturing of high-end bearings for use in extreme environments presents a unique set of challenges. Traditionally, the production of precision mechanical components using high-performance alloys like Inconel®, Stellite®, Invar®, and titanium is not only technically demanding but also economically prohibitive on a low-volume scale.
Machining and finishing these heat-treated materials from billet form can escalate costs and incur technical difficulties, making the process inefficient for small-batch, high-precision applications. And the capital expenditure required for conventional processing methods—such as forging, stamping, and die tooling—is significant, and any redesign necessitates a costly reinvestment in tooling.
Hybrid manufacturing effectively circumvents these challenges, offering a more flexible and cost-efficient solution for those jobs that demand high precision, low volumes, and specialty materials.
Hybrid Manufacturing: The All-in-One Solution
Hybrid manufacturing combines the design flexibility of additive manufacturing with the material availability of welding wire and the precision machining of CNC subtractive manufacturing. This integrated approach is particularly advantageous for producing bearings intended for extreme environments, where complex geometries and high-performance materials are required.
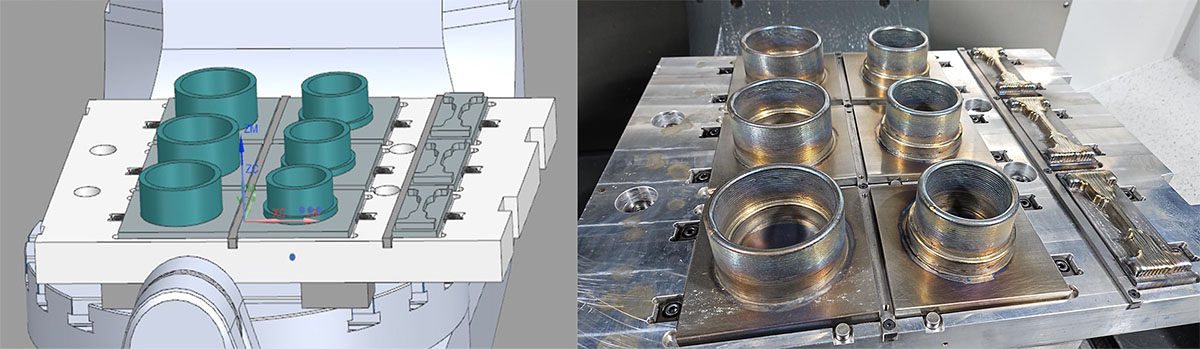
A composite image showing a bearing and coupon simulation (left) and the finished Inconel® 718 prototypes before removal from the fixture. These are bearings for extreme environments designed for the rigors of space exploration. © Hybrid CNC Parts, Inc.
Wire-Laser Metal Deposition (w-LMD)
One type of hybrid manufacturing is wire-laser metal deposition, or w-LMD. Also referred to as direct energy deposition, w-LMD is a 3D printing method that fabricates components by melting wire feedstock via a laser as it’s deposited, layer by layer.
w-LMD is particularly well-suited for handling the unique thermomechanical properties required for bearings destined for extreme environments. Not only does it enable the creation of complex, near-net-shape parts, but also significantly reduces material waste when compared to traditional manufacturing.
A key advantage of w-LMD is the ability to create functionally-graded materials. By “weaving” multiple alloy wires together during the manufacturing process, bearings can be engineered with tailored properties that transition smoothly from one material to another.
This capability is essential for applications where different sections of the bearing are exposed to varying environmental conditions, such as the transition from high-temperature regions to areas requiring enhanced wear resistance.
CNC Subtractive Machining
After the additive w-LMD process, a CNC machine removes excess material and creates the surface finishes necessary for precise tolerances. This subtractive process is critical for refining the final dimensions and ensuring that the bearings meet requirements.
A huge advantage of w-LMD hybrid manufacturing is the ability to seamlessly switch between additive and subtractive abilities within the same setup. This all-in-one system enables rapid design changes and allows for complex geometries that would be unattainable with traditional manufacturing methods alone.
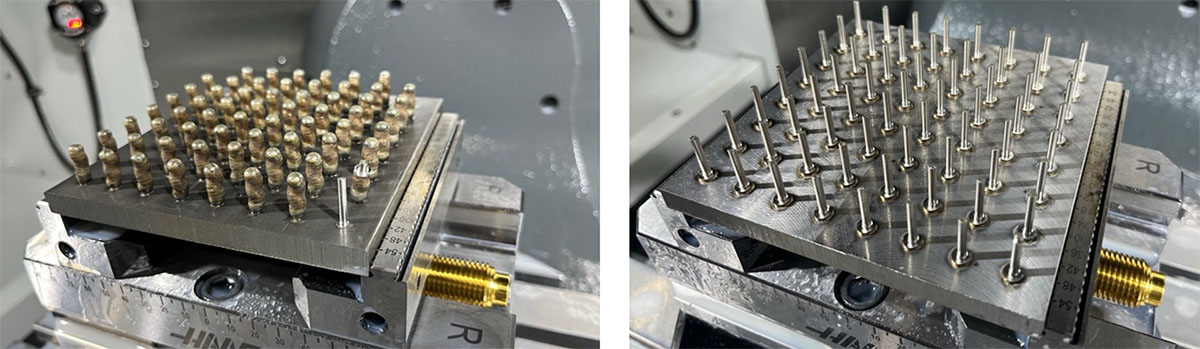
Bearings for extreme environments mean balls or rollers designed for these conditions. These rollers are seen post-additive manufacturing (left) and after subtractive manufacturing during the hybrid manufacturing process. © Hybrid CNC Parts, Inc.
The Hybrid CNC Parts Process
Hybrid CNC Parts employs a hybrid manufacturing approach that integrates these advanced techniques, in order to create bearings from high-temperature, corrosion-resistant materials. Our approach minimizes waste and allows for small batches of high-performance bearings to be manufactured efficiently.
Step 1: Material Selection
High-performance superalloys, like Inconel and Stellite, are capable of withstanding the high temperatures, corrosive environments, and mechanical stresses experienced by these extreme environment bearings.
For example, Inconel 718 is a nickel-chromium superalloy known for its excellent high-temperature strength and resistance to oxidization and corrosion. Stellite 6 is a cobalt-chromium alloy full of complex carbides that offer superior wear and corrosion resistance, making it ideal for applications where these factors are critical.
Material selection plays a crucial role in engineering the best bearing for a particular environment, or range of conditions that may be experienced.
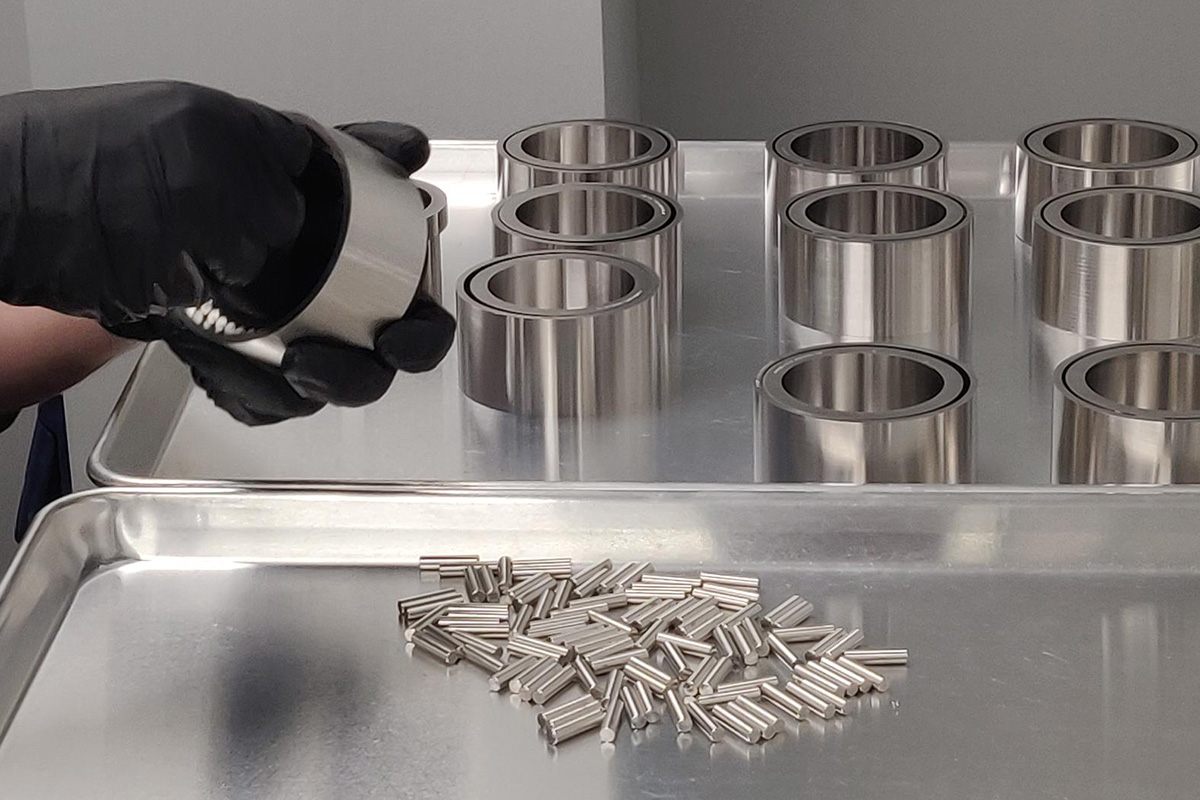
Stellite® rollers being loaded into hybrid manufactured bearing races. © Hybrid CNC Parts, Inc.
Step 2: Hybrid Manufacturing
Our use of w-LMD hybrid manufacturing and expertise in mechanical engineering allow us to additively manufacture complex bearing geometries with precise control over the material’s microstructure.
Parts are built to near-net-shape, and alloys that require heat treatment can actually be hardened in-situ using this laser-based process.
Our experience with engineering functionally-graded components using our proprietary process means we can weave multiple alloys together during manufacturing, creating gradient materials and multi-material bearings that are better able to handle the transition between different environment conditions.
After the additive process, we employ 5- or 3-axis CNC machining to achieve the tight tolerances and surface finishes required for high-performance bearings. This step is essential for ensuring the bearings operate smoothly under the sever conditions they’ll encounter.
Step 3: Post Processing
Post processing is a critical stage, involving any additional heat treatment to optimize the mechanical properties of the alloys and grinding to meet precise specifications.
Heat treatment ensures that each bearing achieves the necessary hardness and wear resistance while maintaining the required flexibility and strength.
Solid lubricants may be integrated at this stage as a solution to the problem of how to lubricate in extreme environments.
These solid lubricants are specifically engineered to provide long lasting, reliable operation where traditional lubrication methods fall short, such as in space or deep-sea applications.
Step 4: Testing and Validation
To ensure that our bearings meet the highest standards of performance, we subject them to rigorous testing, including mechanical and metallurgical analyses.
These tests are conducted according to our quality control program, ensuring that the process parameters for hybrid manufacturing are controlled and that the final products are reproducible and reliable.
Witness Coupons
As part of the testing process, we manufacture associated “witness coupons” alongside the bearing components. These test coupons are produced with the same process parameters—laser power, raster speed, feed rates—as the bearings themselves.
Each coupon undergoes destructive testing to measure mechanical properties such as Young’s modulus, yield strength, ultimate tensile strength (UTS), and elongation, as well as creep and fatigue in select cases. The results from these tests are compared against benchmarks and datasheets to ensure that each batch meets the desired material characteristics.
This rigorous validation process is critical for confirming that the material properties achieved through w-LMD align with industry standards and customer expectations.

An example of the process and the performance of the coupon compared to benchmark data. The custom fixture (left) performs an ASTM E8 tensile test on the coupon, and we compare the results to previous benchmarks and expected results for UTS and yield (right). The results demonstrate that this witness coupon satisfies the requirements. © Hybrid CNC Parts, Inc.
Bearings for Extreme Environments Performance
Our hybrid manufacturing process represents a significant advancement in the production of high-performance bearings for extreme environments. By combining the strengths of additive and subtractive manufacturing techniques, we can deliver components that are not only more cost-effective but also capable of meeting the exacting demands of the most challenging applications.
Through meticulous material selection, innovative manufacturing processes, and rigorous testing, Hybrid CNC Parts ensures that every bearing we produce is engineered for success.
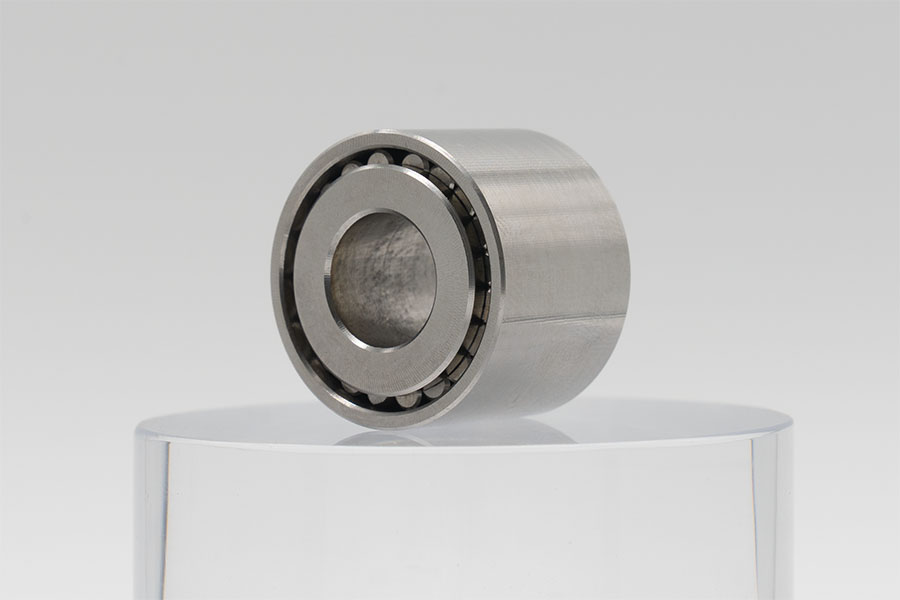
An completed Inconel® bearing engineered for NASA missions in extreme environments. © Hybrid CNC Parts, Inc.
Not All Bearings Are Made Equal
Advanced industries with specialized requirements often can’t rely on commercial, off-the-shelf bearings to perform optimally in extreme environmental conditions. They melt, wear down, deform, or grind to a halt. Such a small component can make or break your project (quite literally).
This is where Hybrid CNC Parts steps in. We specialize in developing high-performance bearings that thrive under the most punishing conditions. Our cutting-edge hybrid manufacturing techniques allow us to create components that are not only durable but also exhibit exceptional performance under the most extreme circumstances. By combining advanced materials with innovative manufacturing processes, we are redefining what is possible in bearing technology.
Contact us today to learn more about how our custom-engineered bearings can meet the specific needs of your most challenging applications. Let us help you drive innovation and success in extreme environments with components designed for the future.