What is Hybrid Manufacturing?
Hybrid manufacturing is a process that combines additive (3D printing) and subtractive (CNC machining) operations. When we think about hybrid manufacturing it’s usually in reference to fabricating with metals, but hybrid manufacturing is picking up with polymers as well.
There are several types of metal additive processes, including powder-bed fusion, filament bound, and cold spray. Each process has its use, and not all metal additive processes will be ideal for all situations.
For this article, we’ll be focusing on wire-laser metal deposition (w-LMD) as the metal additive method of choice. W-LMD has significant advantages compared to the other methods, including:
- More efficient use of raw materials
- Highly customized and complex components
- Functional grading for multi-material parts
- Raw materials that are safe to handle
- A reliable, USA-based supply chain
W-LMD hybrid manufacturing uses lasers to melt wire feedstock one layer at a time, building up a part to near-net shape. CNC subtractive processes, which are integrated into the same system, refine it. Both the additive and subtractive manufacturing occur without having to change the setup, making it a fast, efficient, and precise production process.
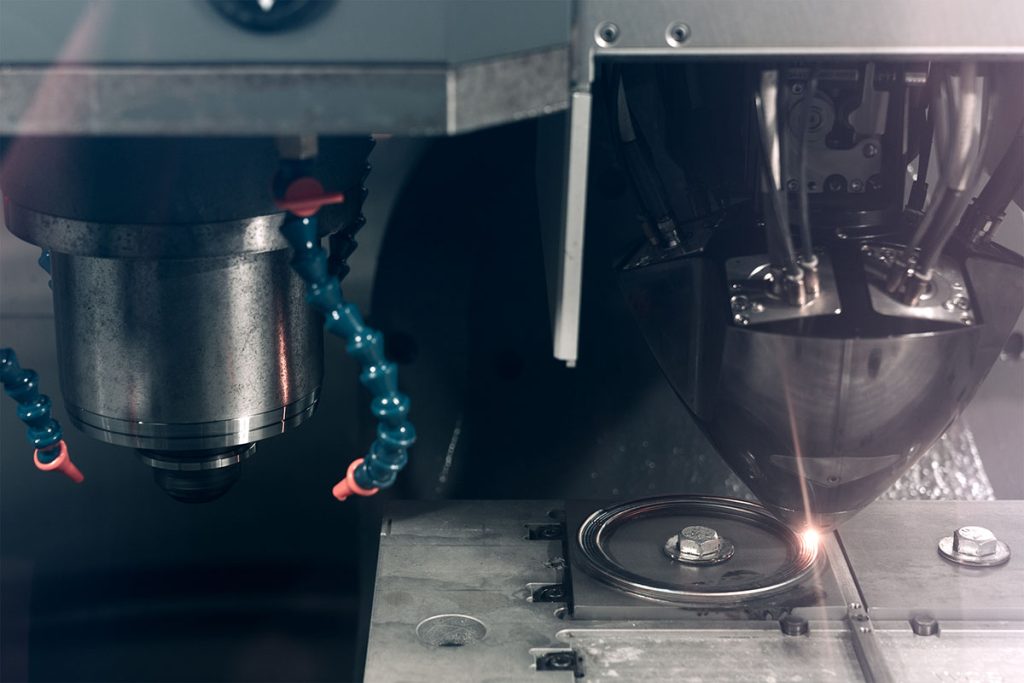
The interior of a Hybrid CNC Parts’ w-LMD hybrid system consisting of a Haas CNC (left) and Meltio w-LMD unit. © Hybrid CNC Parts.
In this post
This article will discuss how industries that need components or tooling for demanding applications, like aerospace, energy, manufacturing, defense, and performance automotive can improve ROI with hybrid manufacturing.
We’ll first look at what ROI is and why it matters, and then dive into the ways w-LMD hybrid manufacturing can improve it. To help illustrate, we’ve included a detailed example ROI calculation for a traditional- vs hybrid-manufactured mold tool.
Why Return on Investment Matters
Return on investment (ROI) is a critical measurement for understanding profitability and efficiency, whether it’s for production, technology, finances, or even that gym membership you got as part of your New Years resolutions.
In industry, it’s used to not only understand if investments in tooling, materials, and processes are worthwhile, but can be applied to stakeholder buy-in, supporting company values, and indicating if a course correction is needed—before it’s too late.
The following are some of the top advantages to tracking and using ROI:
- Measures Profitability: ROI helps you understand if your investments—in technology, machinery, your IRA—are effective by comparing the profits generated relative to the costs.
- Justifies Capital Expenditure: ROI provides an understanding of the value derived from your investment. It’s also used for validation—ensuring that new product line, tooling, or facilities upgrade—aligns with a business’s financial goals.
- Drives Operational Efficiency: ROI provides performance benchmarking and highlights areas in need of optimization. It also helps guide continuous improvement in operations, waste management, and throughput so that you can ensure your investment is being maximized.
- Supports Risk Management: Understanding ROI reduces uncertainty by quantifying potential gains before committing to investments. It also helps assess projects and allows for pivots if ROI is below expectations.
- Promotes Sustainability: Investments in sustainable practices often lead to reduced costs in the long run, such as decreased energy usage and material savings. It demonstrates a commitment to sustainability, which can attract customers and improve your market position.
- Builds Stakeholder Confidence: High ROIs signal strong management and effective resource use. It also validates decisions to employees and leadership and fosters a culture of data-driven growth.
ROI offers a multifaceted analysis that measures how effective a business is at operating, adapting, and growing. Ensuring a good ROI means long-term profitability and a competitive edge.
ROI Challenges with Traditional and Additive Manufacturing
Now that we have an idea of why ROI matters, in order to better understand why hybrid manufacturing can improve your ROI, let’s explore the alternatives of traditional manufacturing and straight up additive manufacturing and their challenges related to profitability and efficiency.
Traditional Manufacturing is Reliable—But Slow, Expensive, and Bottlenecks Innovation
When it comes to complex, tailored, specialty material components, the setup and material costs associated with traditional subtractive manufacturing (milling, drilling, etc.) can be costly.
Factors affecting traditional manufacturing ROI include:
- Extensive Tooling Requirements: Manufacturing complex parts often requires custom molds, dies, or fixtures, which are expensive to design and produce. It usually takes multiple tool changes and potentially specialized tools to create components with sophisticated geometries, all adding to overall setup time and expense.
- Material Waste: Material prep is another area where traditional manufacturing falls short. If your part calls for high-performance or non-standard materials, it can be costly and challenging to prepare for production. Initial runs often generate a lot of waste as machines are fine-tuned, and subtractive-only methods rely on starting with a block and removing the excess—wasting a large portion of raw material.
- Long Production Cycles: Traditional manufacturing can also be time intensive, with intricate set ups and labor increasing costs. Adjustments may involve several iterations, which take time and additional setups or tooling. Production times are generally long.
- Limited Flexibility: Subtractive-only setups are usually designed for specific parts, making iterations or modifications costly to undertake. Switching from one part to another involves repeating many steps, eating up time and costs. Highly-intricate geometries or internal structures are often impossible to achieve with traditional manufacturing methods alone.
Additive Manufacturing Alone is Innovative—But Limited
While additive manufacturing is a part of hybrid manufacturing, using standalone additive systems have their own ROI challenges when compared with hybrid methods.
Using only additive manufacturing often means your parts will less refined or complex. For more finished components, you will still need to use traditional manufacturing methods, which will involve many of the challenges already discussed, such as tooling, setup, and labor expenses—all contributing to additional costs and decreased efficiency.
The Advantages of Hybrid Manufacturing
The rapidly evolving needs of modern industries require improving just about all aspects of operation, from reduced lead times to better scalability. W-LMD hybrid manufacturing’s unique advantages can address these ever-changing needs in several key areas, in turn improving efficiency, performance, innovation, and—ultimately—ROI.
Key Ways to Improve ROI with Hybrid Manufacturing
Hybrid manufacturing contributes to improving ROI in several crucial areas:
- Increased Flexibility and Customization: Hybrid manufacturing allows for rapid prototyping, even for components with complex geometries. It supports the production of customized solutions at scale, ranging from patient-specific medical implants and customized automotive parts to tailored molds for plastic manufacturing.
- Integrated Functionality: Together with customization is the ability to design for integrated functionality. Think molds with internal conformal cooling channels that would be impossible to fabricate using subtractive-only methods. Targeted functional grading can enhance specific parts of components, improving durability and performance.
- Enhanced Efficiency and Productivity: Precise and efficient, hybrid manufacturing enables faster production cycles. It streamlines processes by eliminating the need for multiple setups, thereby reducing downtime and increasing throughput.
- Cost Reduction: Waste is a huge concern, especially when using expensive materials. Since parts are produced near net shape, hybrid manufacturing minimizes material waste—significantly lowering material costs. It also reduces tooling costs, since it eliminates the need for costly molds and dies in early production stages.
- Improved Product Quality: Hybrid manufacturing—particularly w-LMD—produces intricate, durable parts with high accuracy. W-LMD is also capability of combining materials with varying properties to enhance product performance and longevity.
- Scalability: Hybrid manufacturing facilities transitioning from prototypes to manufacturing at scale without requiring entirely new workflows or equipment.
Sustainability and Resource Optimization: W-LMD hybrid manufacturing reduces material waste and energy consumption compared to traditional manufacturing alone. - Competitive Advantage: Hybrid manufacturing is used to create innovative products with improved functionality, reduced weight, and higher durability. It is an invaluable tool used to adapt quickly to changing customer and market demands.
Hybrid manufacturing empowers industries to achieve better ROI by increasing cost-effectiveness, improving efficiencies, and driving innovation, making it indispensable in today’s competitive and rapidly evolving market.
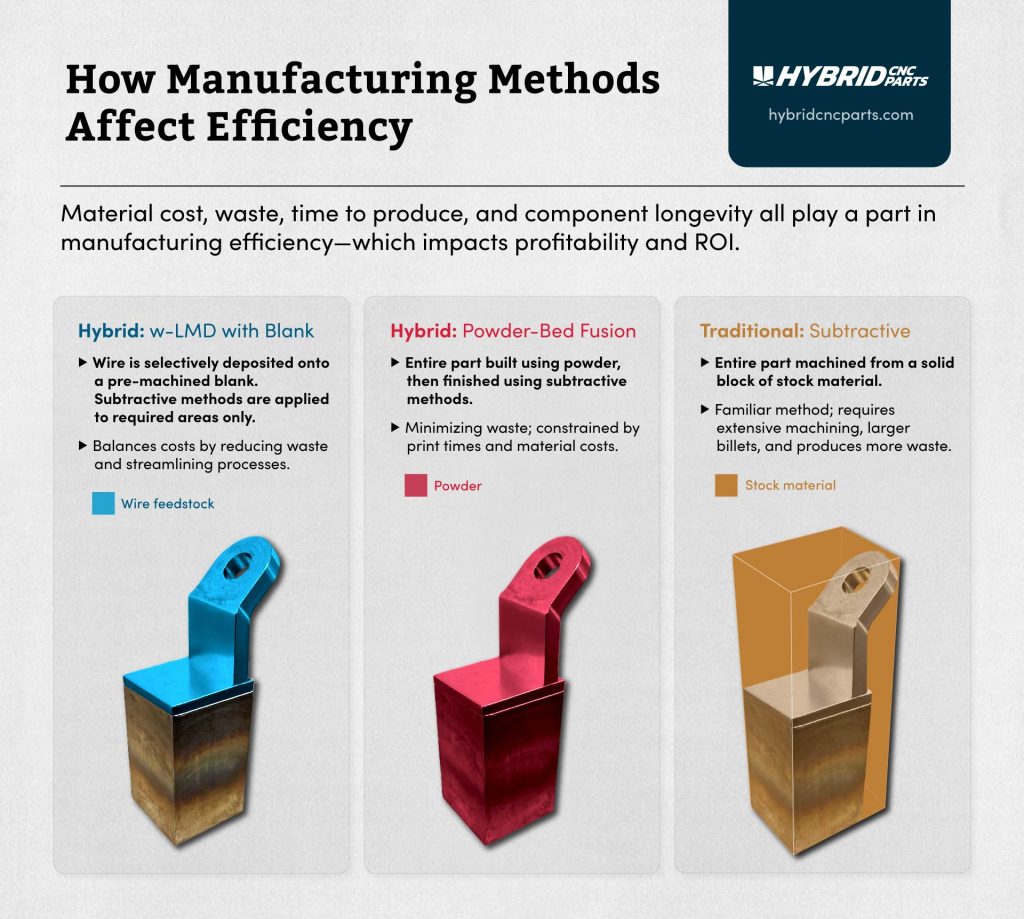
How manufacturing methods affect efficiency—and ROI. A visual comparison of w-LMD, powder-bed fusion, and traditional subtractive methods. © Hybrid CNC Parts.
Wait. Isn’t Hybrid Manufacturing Expensive?
Yes and no.
We cover this issue in more depth in our article on More Durable Molds that Last Longer with Advanced Manufacturing, but in a nutshell: designing for w-LMD hybrid manufacturing can be more expensive than traditional manufacturing, especially if the component is complex.
However, the long-term cost savings associated with reduced material waste, improved durability, shorter lead times—and everything else mentioned above—are well worth the initial investment.
Deep Dives: How w-LMD Hybrid Manufacturing Improves ROI
Let’s take a closer look at a few of the ways w-LMD hybrid manufacturing can improve ROI through reducing both short- and long-term costs as well as driving innovation.
Short Term Savings: Less Material Waste
Using wire feedstock allows for a lot less material waste, since parts are created near-net shape. For components with complex designs—like turbine blades, impellers, and heat exchangers—hybrid processes allow manufacturers to build up material only where it’s needed, reducing waste and enabling advanced shapes.
W-LMD hybrid manufacturing can be used in a couple of ways, both of which produce less material waste than traditional methods.
- 100% Wire-Laser Metal Deposition + Machining: Additive manufacturing builds the part layer by layer with wire feedstock. Precision machining is then used to refine the final shape. Since the part is near-net shape, little material is wasted.
- Pre-Machined Blank + Hybrid Manufacturing: Starting with pre-machined stock and then using w-LMD reduces the material added via deposition, while still allowing for intricate designs. This approach balances efficiency and cost.
These methods not only save material but also reduce machining time, leading to faster production and lower costs overall. Additionally, hybrid manufacturing enables iterative prototyping, allowing engineers to refine designs quickly and bring products to market faster.
When working with expensive materials like Inconel, Stellite®, or titanium, every gram counts.
Consider an impeller used for moving fluid in an industrial compressor:
- Machining from Solid Block: This approach wastes up to 60% of the material, significantly increasing costs.
- W-LMD Hybrid Manufacturing: By building the blade up layer by layer, hybrid manufacturing reduces waste to under 10%, saving thousands of dollars per part.
The cost savings go beyond material. Hybrid manufacturing reduces the number of setups required, consolidating additive and subtractive operations into a single process. This minimizes labor costs, shortens lead times, and reduces the risk of errors during re-fixturing.
Innovation through Design Freedom
A huge advantage with w-LMD hybrid manufacturing is the design freedom it offers. Intricate geometries, internal structures, and enhanced functionalities are often difficult or impossible to achieve with traditional methods alone. If available, these features could provide lighter, stronger, more durable components—boosting overall efficiency and quality, and providing superior competitive advantages.
W-LMD hybrid makes these design options possible. Everything from internal conformal cooling channels to a functionally-graded Inconel® layer can make components last longer and perform better.
By removing design restraints, room is made for innovation and the increases in ROI that it can bring.
Long Term Savings: Longer-Lasting Parts
The long-term cost savings associated with w-LMD hybrid manufacturing can be measured against the combination of material savings, efficiency gains, and lower maintenance costs.
Here’s how w-LMD hybrid manufacturing drives value:
- Material Savings: Use less material, spend less money. For high-value alloys, save up to 50% in material costs.
- Efficiency Gains: Shorter cycle times and higher throughput.
- Reduced Maintenance Costs: Longer-lasting parts mean fewer replacements and less downtime.
By combining these factors, w-LMD hybrid manufacturing allows businesses to achieve better financial outcomes while maintaining superior product quality. For companies working with expensive materials or high-precision components, the ROI becomes clear after just a few production runs.
Use Case: Improving ROI with Hybrid Manufactured Mold Tooling
Mold tooling is a perfect example of how w-LMD hybrid manufacturing can enhance ROI through performance improvements. Injection molds with internal conformal cooling channels—designed to follow the contours of the mold cavity—enable better heat transfer, resulting in faster cycle times, higher-quality parts, and fewer mold replacements.
While these molds may cost more to produce upfront due to their complex designs, the benefits on the back end are significant:
- Reduced Cycle Times: Conformal cooling channels improve thermal efficiency, reducing the time needed for parts to cool. This allows manufacturers to produce more parts per hour.
- Longer Tool Life: Molds using wear-resistant materials last longer, reducing maintenance costs and downtime.
Detailed Calculation
Let’s look at an example of the gains and long-term cost savings associated with a w-LMD hybrid mold.
Imagine an injection mold tool used to produce a small plastic part. Let’s assume the following baseline data:
- Annual Sales: $1 million
- Gross Margin: 40% (i.e., $400,000 gross profit)
- Current Mold Cycle Time: 30 seconds
- Production Time: 24/7, 85% efficiency (7,446 hours/year or 446,760 minutes/year)
- Annual Cycles: 894,000 cycles/year
The current mold is maxed out, running continuously to meet demand. To increase production, you face two options:
- Order a new conventional mold to run in another set up. Assume this mold costs $100,000
- Invest in a w-LMD hybrid-manufactured mold with conformal cooling to improve efficiency using the existing press. Assume this mold costs $130,000 because of the increased complexity.
Conformal cooling in a hybrid mold can reduce cycle time by 35%. This reduction brings the cycle time down to 19.5 seconds, which would increase annual production to 1.374 million cycles—resulting in a 54% increase in output compared to the current mold.
With a 54% increase in output, annual sales increase from $1 million to $1.54 million. The gross margin also increases proportionally:
- Original Gross Profit: $400,000
- New Gross Profit: 40% of $1.54 million = $616,000
This difference represents a $216,000 annual increase in gross profit.
The additional $30,000 investment for w-LMD hybrid manufacturing can be paid back quickly due to the increased efficiency, although we should also account for the increased usage of plastic and energy associated with making more parts.
Now, let’s calculate the net profit increase over 3 years:
- Total Profit Increase: $648,000
- Additional Resin Cost: $162,000
- Additional Electricity Cost: $30,000
Thus, the 3-year net profit increase from investing in a hybrid mold is $456,000.
Summary of ROI Calculation
Metric | Value |
---|---|
Annual Sales Increase | $540,000 |
Annual Gross Profit Increase | $216,000 |
Hybrid Mold Cost | $130,000 |
Payback Period | 2 Months |
3-Year Gross Profit Increase | $648,000 |
3-Year Additional Costs (Resin + Energy) | $192,000 |
3-Year Net Profit Increase | $456,000 |
Getting Started with Hybrid Manufacturing
Hybrid manufacturing offers transformative benefits, but getting started requires a strategic and well-informed approach. To maximize the potential of hybrid methods, consider the following key steps:
Assess Your Current Manufacturing Process
Begin by evaluating your existing manufacturing workflows, capabilities, and challenges. Identify bottlenecks, inefficiencies, or limitations in producing complex geometries, multi-material components, or high-precision parts. This step is critical for understanding where hybrid manufacturing can provide the greatest impact, whether it’s reducing lead times, improving part quality, or lowering overall production costs.
Collaborate with Experts
Hybrid manufacturing can involve a steep learning curve, especially for organizations new to additive or integrated processes. Partnering with experienced consultants, technology providers, or hybrid manufacturing experts can help bridge the knowledge gap. These professionals can guide you in optimizing your workflows, training your team, and implementing best practices to ensure a smooth transition to hybrid manufacturing.
By systematically assessing your needs and leveraging the right technologies and expertise, you can unlock the full potential of hybrid manufacturing, driving efficiency, innovation, and return on investment.
Conclusion
W-LMD Hybrid manufacturing represents a transformative approach to optimizing return on investment in modern manufacturing. By combining the precision and design flexibility of additive manufacturing with the efficiency and scalability of traditional methods, w-LMD hybrid manufacturing significantly reduces production costs, minimizes waste, and accelerates time-to-market.
This technology not only enables the production of complex parts with enhanced material properties but also addresses the high setup costs and limitations of standalone manufacturing processes.
For businesses aiming to stay competitive in a rapidly evolving industry, adopting w-LMD hybrid manufacturing is not just an operational upgrade—it’s a strategic investment in long-term profitability and innovation.
Have Questions about Hybrid Manufacturing?
Contact us with your questions! As experts in w-LMD hybrid manufacturing, we are here to help you achieve your manufacturing goals—including finding a solution that works best for your business.
Why Hybrid CNC Parts? We offer fully-integrated design, engineering, and production services focusing on high-performance materials, custom components, and low-volume orders.
Not ready to dive in?
Keep exploring what hybrid manufacturing has to offer:
- There’s more article on advanced and hybrid manufacturing on our blog.
- Read up on our hybrid manufacturing services.
- Check out our FAQs.
Contents
- What is Hybrid Manufacturing?
- Why Return on Investment Matters
- ROI Challenges with Traditional and Additive Manufacturing
- The Advantages of Hybrid Manufacturing
- Deep Dives: How w-LMD Hybrid Manufacturing Improves ROI
- Use Case: Improving ROI with Hybrid Manufactured Mold Tooling
- Getting Started with Hybrid Manufacturing
- Conclusion
- Have Questions about Hybrid Manufacturing?
Contents
- What is Hybrid Manufacturing?
- Why Return on Investment Matters
- ROI Challenges with Traditional and Additive Manufacturing
- The Advantages of Hybrid Manufacturing
- Deep Dives: How w-LMD Hybrid Manufacturing Improves ROI
- Use Case: Improving ROI with Hybrid Manufactured Mold Tooling
- Getting Started with Hybrid Manufacturing
- Conclusion
- Have Questions about Hybrid Manufacturing?