The cost of conventional moldmaking
At the beginning of any plastic forming project, whether it’s blow molding or injection molding—or even (especially?) thermoforming—there always seems to be that sticker shock moment when the cost of the mold is quoted.
The price of injection molding in particular—with its complex tooling, need to withstand high production pressures, and a propensity for using steel —can act as a major barrier to spinning up a new product line or embarking on an innovative project.
And cost isn’t the only barrier being put up by conventionally-made molds in industries that are looking to innovate, improve efficiencies, and see a decent return on investment.
In this article, we’re going to explore two important areas affecting mold-reliant industries:
- The limitations imposed on molding industries when they use conventionally-manufactured tooling.
- How hybrid manufacturing offers an exciting alternative option that addresses these limitations and then some.
How conventional moldmaking is limiting industry
To understand the limitations of conventionally-made molds, we need to look at their affects on the industries that rely on them heavily, like injection and blow molding.
Conventional molds are typically machined from solid blocks of aluminum or steel, and assembled with components like cavities, back plates, pins, bushings, and connectors. This type of machining is subtractive-based, meaning material is removed until the final form is achieved.
Subtractive manufacturing is common, reliable, and familiar, but it also introduces several limitations:
- Material waste and high costs: Machining large blocks of material into finished molds generates significant scrap, particularly when using premium materials like expensive tool steels. Throwing away a significant amount of material makes this method inherently inefficient and costly.
- Cooling inefficiencies: Cooling a mold as part of the production process is vital to ensure proper product forming and release. Properly cooled molds decrease cycle time and ensure minimal warping and part rejection. With subtractive manufacturing, cooling channels are usually gun-drilled straight into the mold or back plates, and for complex or multi-cavity molds, this method can lead to thermal inefficiency and undesirable thermal gradients.
- Wear and fatigue: Most molds undergo wear in high-stress regions, like the parting lines in blow molds, or the gates and ejector pin regions of injection molds. Because these components are traditionally manufactured from a single material, localized fatigue can lead to frequent repairs, replacements, and downtime.
- Design constraints and lead times: Complex designs, like undercuts or intricate geometries, require multi-part molds, which add to design and fabrication time. Large molds can take months to produce, even once a final design is determined.
Solving moldmaking challenges with hybrid manufacturing
If traditional moldmaking techniques are less than ideal for creating more efficient and durable molds, what’s the alternative? The answer lies in combining conventional manufacturing with advanced methods.
Hybrid manufacturing is the integration of additive manufacturing with traditional subtractive processes, all within a single system. This combination allows for greater moldmaking efficiency and flexibility, and can improve mold performance through innovative designs and high-performing materials that aren’t feasible when relying on solely conventional manufacturing methods.
Benefits of hybrid manufactured molds include:
- Reduced material waste: Hybrid manufacturing builds parts layer by layer, depositing material only where it’s needed, creating the component in near net shape and then processing it as-necessary afterwards. This process minimizes material waste, making expensive tool steels and even superalloys like Inconel® and Stellite® more cost-effective.
- Conformal cooling: Conformal cooling channels are internal structures that hug the shape of a mold cavity. They’re more efficient since they can be placed an equal distance from the part for the entire length of the mold, removing heat where and when it’s needed and avoiding thermal gradients.
- Multi-materials for enhanced durability: Hybrid manufacturing unlocks the ability to target specialized materials in areas where molds need it most. For example, an area that experiences a lot of friction could benefit from a specialized wear-resistant material in that one specific location, while the rest of the mold can be made from more economical materials. Targeted enhancements can extend the overall lifetime of the tool without breaking the bank.
- Shorter lead times: Hybrid manufacturing doesn’t require a lot of tool changing, which saves on time and costs. Its additive/subtractive technique is faster and more efficient than conventional manufacturing, and allows for rapid prototyping without drastically-long lead times. Faster iterations mean more freedom to innovate and reduced lead times.
Trade-offs:
Conventional vs Hybrid Manufacturing
Every manufacturing method involves trade-offs, and hybrid manufacturing is no exception. Here’s a quick comparison to help you decide which approach is best for your needs.
Conventional manufacturing
Pros
- Familiar moldmaking processes
- Accessible expertise through traditional manufacturers
- Low initial equipment costs
Cons
- High material waste due to solely subtractive manufacturing
- Long lead times
- Limited capability for innovation
- Frequent maintenance and replacements due to wear and tear
Hybrid manufacturing
Pros
- Reduced material waste with near net shape manufacturing
- Innovation-ready with ability to create complex mold cavities
- Enables integrated conformal cooling and other internal features
- Specialty materials can be applied to specific areas to improve durability where it’s needed the most
Cons
- Higher up-front investment for design services and specialty materials
- Not a commonly available manufacturing method
- Learning curve for integration/adoption within processes
Industries that benefit from hybrid moldmaking
Blow molding and injection molding account for a massive amount of consumer and industrial products, from milk jugs and toys to trash cans, lawn furniture, medical devices, automotive components—all the way up to aerospace components.
There’s nothing inherently wrong with using conventionally-made molds. They’ve been getting the job done since at least 4,000 B.C., with castings of ancient copper axe heads found in Europe. But old school doesn’t necessarily equate to efficiency. And in industries that rely heavily on molds to make their products, efficiency equals cost savings.
Here are a few industries that could increase efficiencies by switching to hybrid manufacturing for their moldmaking, and what those benefits could look like:
Consumer Packaging: Conventional molds used for high-speed blow molding wear out quickly and require frequent replacements, driving up maintenance costs. The fast-paced nature of consumer goods production benefits from hybrid molds that incorporate wear-resistant inserts that strategically extend tool life.
Medical Devices: Conventional moldmaking struggles to meet the precision requirements for small, intricate parts, resulting in a higher rejection rates of medical devices. The ability to create sophisticated, precise geometries with hybrid manufacturing could increase the acceptance rate of this essential equipment.
Automotive: Traditional molds can’t keep up with the growing demand for lightweight parts and advanced geometries that are desired in the automotive sector, leading to higher costs and longer production times due to the amount of work required when these types of molds are made conventionally. Hybrid manufacturing can help automotive manufacturers meet tight production schedules by reducing cycle times through faster tool changes and could more easily provide the complex geometries being sought after.
Aerospace: Aerospace manufacturers face challenges with heat dissipation in molds, and conventional cooling channels are insufficient for the complex geometries that could solve these issues. The ability to efficiently create internal structures, like conformal cooling channels, with hybrid manufacturing could help aerospace companies manufacture their components more efficiently. It could also unlock performance innovations with its ability to create more unique and complex designs.
Of course, different industries have unique requirements for molds. Some may be perfectly fine with conventionally-made tools or the downtime that comes with frequent repairs and replacements.
However, for those industries that demand durability, efficiency, and precision, hybrid manufacturing offers a viable moldmaking alternative.
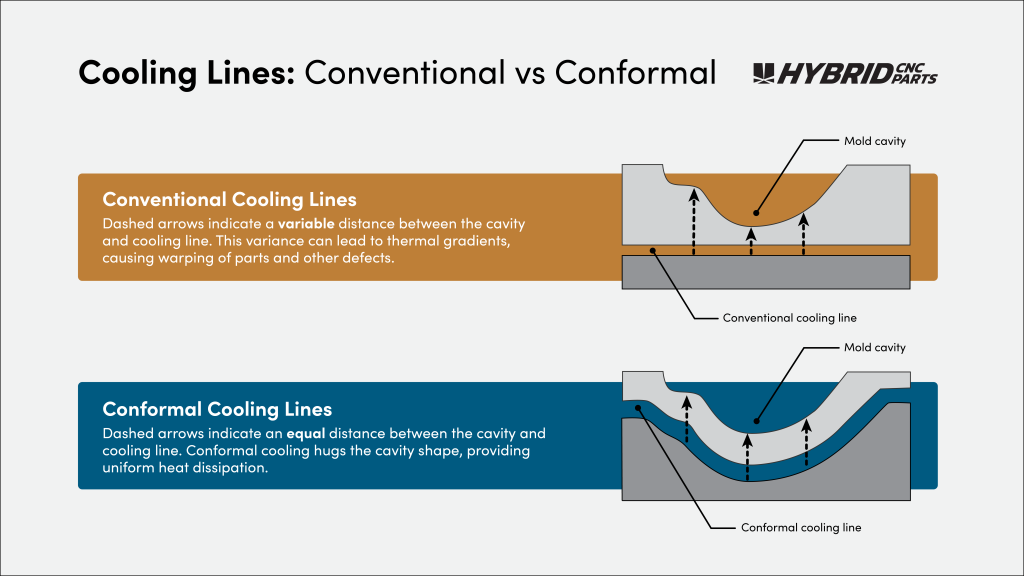
Image: The difference between conventional cooling lines (top) and conformal cooling lines (bottom). Conventional cooling lines are normally drilled as straight channels, resulting in uneven heat distribution due to the variable distance between the line and mold cavity. This variability can lead to thermal inefficiency, creating warped products. Conversely, conformal lines follow the shape of the cavity. This design speeds up the cooling process by uniformly removing heat and ensuring that parts are not damaged. © Hybrid CNC Parts.
Is it time to switch to hybrid?
If this article is the first time you’ve heard of hybrid manufacturing for moldmaking, you probably have a lot questions. Luckily for you, we love discussing hybrid technology and how it can best benefit our customers.
Here are a few options for what to do next:
- We have a previous blog post on improving the durability of molds with hybrid manufacturing.
- Our dedicated page on hybrid manufacturing goes into more detail about the process, the benefits, and why we use wire-laser metal deposition as our additive method of choice.
- If you’re ready to discuss how hybrid can work for you—or have questions about the technology, our services, or any of the above—give us a shout.
Contents
Contents