Understanding Superalloys
Superalloys. The name alone suggests something extraordinary—materials engineered to excel where others fail. Yet despite their reputation, these alloys are often misunderstood, even by experienced engineers and manufacturers.
Requests for materials like Inconel® are common, driven by its fame in extreme applications. But when we ask why it’s been chosen, the answer is often based more on hearsay than a true understanding of its properties. Yes, Inconel is strong and excels under heat and stress—but did you know it’s not as hard as some grades of stainless steel, and can end up costing much more than it’s worth to machine it?
And materials like Stellite®? Mention it, and you’ll likely get puzzled looks or even hear, “I hate that stuff.” That’s usually because people haven’t had the chance to work with it—or struggled when they did.
The truth is, materials like Inconel, Stellite, and other superalloys are remarkable, but only when used correctly. They excel in the areas that matter most—heat resistance, corrosion resistance, and mechanical strength. But they’re also notoriously difficult to machine, weld, and process. To truly leverage these materials, you need skill, experience, and the right equipment—without which, you risk skyrocketing costs and diminished returns.
What we’ll discuss
In this article, we’ll guide you through a small slice of the world of superalloys, breaking down why they perform so well in extreme environments and what makes them so challenging to work with. We’ll explore a few key categories, including nickel-based workhorses like Inconel and the less-known but incredibly durable cobalt alloy Stellite. We’ll weave in a little material science to give you a fuller picture of why these materials are special, what they’re best suited for, and whether they’re the right fit for your next project.
More importantly, by the end of this journey, we want you to take away one key point: working with superalloys isn’t just about choosing the right material for your application—sometimes choosing the right material requires balancing engineering needs, manufacturing constraints, and cost limitations. Whether you’re designing aerospace components, turbine blades, or high-wear industrial parts, success depends on expertise in balancing these key issues. And when it comes to superalloys, that’s where we excel.
So let’s dive in and explore what makes these materials “super”—and why, if you’re considering using them, you need a partner who knows them inside and out.
ISO Group S: An Overview of Superalloys
When we talk about superalloys—those materials built to thrive in extreme environments—ISO Material Group S is the classification where you’ll find them. These alloys are the unsung heroes of industries that demand high performance at elevated temperatures, whether it’s deep inside a jet engine or in corrosive chemical reactors. They’re designed to maintain their strength, resist corrosion, and keep performing under stresses that would cripple most other materials.
Superalloys are generally categorized by their primary alloying element: nickel, cobalt, iron, or titanium. While iron-based and titanium alloys are technically part of ISO Group S, they won’t be our focus here. Iron-based superalloys are typically chosen for applications where cost efficiency is more important than extreme high-temperature performance, while titanium alloys are often preferred in weight-sensitive aerospace and biomedical applications. Both are important, but they don’t play in the same league as nickel and cobalt alloys when it comes to handling the highest temperatures and stresses.
So, for this discussion, we’ll concentrate on the materials that are true workhorses in the toughest conditions: nickel and cobalt-based superalloys. These alloys are where you find the pinnacle of high-temperature strength, oxidation resistance, and wear resistance.
Nickel-based superalloys
Nickel-based superalloys are the go-to choice when you need materials that won’t flinch at temperatures above 800°C (1,472°F). These alloys are built for the extremes, with microstructures optimized for maximum performance in high-heat environments. But while they’re incredibly strong at elevated temperatures, they come with a price—they’re notoriously difficult to machine, and their properties can be misunderstood if you’re not familiar with the details.
Nickel-based superalloy properties
- γ (Gamma) Phase Matrix: The foundation of nickel-based superalloys is the γ-phase, a face-centered cubic (FCC) structure that offers solid toughness and flexibility. It’s the “backbone” of these alloys, providing the basic mechanical stability needed to survive high-stress environments.
- γ’ (Gamma Prime) Precipitates: The secret sauce of nickel superalloys lies in the γ’ precipitates, usually composed of Ni₃(Al, Ti). These particles act like internal barriers that block dislocations—tiny defects that cause a material to deform under stress. In simple terms, these precipitates reinforce the alloy, keeping it stable even when subjected to intense heat and mechanical loads.
Nickel-based superalloys are often favored for applications like gas turbines, jet engines, and industrial furnaces, but they’re not without challenges. The very properties that make them valuable—such as high-temperature stability and resistance to creep—also make them a nightmare to machine if you don’t have the right tools or experience.
Cobalt-based superalloys
Cobalt-based superalloys like Stellite and Haynes® alloys may not be as famous as their nickel counterparts, but they hold their own in environments where wear resistance, thermal stability, and corrosion resistance are critical. Unlike nickel alloys, which rely heavily on γ’ precipitates for strengthening, cobalt alloys gain much of their toughness from the base metal itself, supported by stable carbides that provide exceptional wear resistance.
Cobalt alloys are indispensable in high-wear, high-temperature situations. Components like valve seats, bearings, and cutting tools are where these materials shine. But anyone who’s worked with Stellite knows it can be extremely difficult to machine. It’s a material you use when you need something that will last and perform, but it takes specialized knowledge and techniques to work with it efficiently.
Superalloy Properties
The following table demonstrates the relative property applicability of superalloys Inconel and Stellite.
See Materials for an expanded range of alloys.
Material | Lightness | Heat Resistance | Corrosion Resistance | Hardness / Wear Resistance | Example Grades |
---|---|---|---|---|---|
Nickel | – | Inconel® 625 Inconel® 718 Inconel® X-750 Hastelloy® C-276 | |||
Cobalt | – | Stellite® 6 Haynes® 188 Ultimet® |
Nickel
Example Grades:
Inconel® 625 Inconel® 718 Inconel® X-750 Hastelloy® C-276
Lightness: –
Heat Resistance:
Corrosion Resistance:
Hardness/Wear Resistance:
Cobalt
Example Grades:
Stellite® 6 Haynes® 188 Ultimet®
Lightness: –
Heat Resistance:
Corrosion Resistance:
Hardness/Wear Resistance:
Inconel
The workhorse of high-temperature alloys
Inconel is a staple for high-temperature applications in aerospace, power generation, and heavy industry. Its reputation for excelling under extreme heat is well-deserved, but it’s often specified without fully understanding its specific strengths—and its challenges.
High strength at high temperatures
Inconel belongs to a family of nickel-chromium alloys designed to perform at extreme temperatures, where most materials would soften, oxidize, or corrode. But here’s where misconceptions start: while Inconel is undeniably strong at elevated temperatures, it isn’t necessarily harder than some stainless steels. This can lead to confusion when engineers expect Inconel to resist scratching or indentation like a hardened steel might.
For applications like jet engines and power plant turbines, where materials are exposed to temperatures near their melting points, Inconel is an obvious choice. But if you’re considering Inconel purely for its “strength,” make sure you’re not mistaking it for hardness—it’s designed for toughness under heat, not for resisting impact or surface wear like a tool steel.
Machining Inconel: Where the real challenge lies
Here’s where the rubber meets the road. Working with Inconel is notoriously difficult, and it’s often said that machining Inconel feels like cutting through a heat-resistant brick. The reasons are straightforward but non-negotiable:
- Poor thermal conductivity: Inconel traps heat at the cutting edge, causing tools to wear out rapidly if not managed correctly.
- Work hardening: Inconel is infamous for work hardening during machining. If your tooling isn’t up to the task, each pass makes the
material tougher to cut, leading to rapid tool wear and potentially ruining of the work piece.
To machine Inconel successfully, you need specialized cutting tools (usually coated carbide or ceramic), optimized speeds and feeds, and aggressive cooling strategies. Anything less, and you’ll quickly run into problems. This is where expertise counts—having the right knowledge can mean the difference between a smooth run and a frustrating series of broken tools and scrapped parts.
Where Inconel works best
Despite the challenges, Inconel is indispensable in applications that combine high heat, stress, and corrosion. Some of the most common grades and uses include:
- Inconel 718: Known for its resistance to creep and rupture at high temperatures, Inconel 718 is widely used in gas turbines, jet engines, and even some nuclear reactors. It’s the material of choice when components need to withstand both sustained high temperatures and mechanical loads.
- Inconel 625: This alloy is prized for its excellent corrosion resistance in marine environments, as well as its high strength. You’ll find it in chemical processing equipment, seawater components, and anywhere both strength and corrosion resistance are critical.
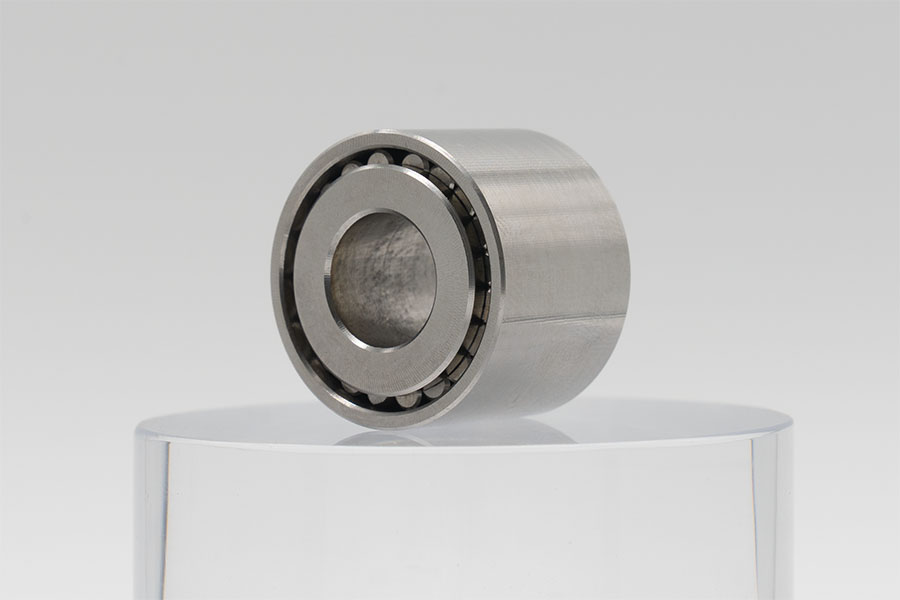
An Inconel® bearing designed for the extreme environments encountered during inter-planetary NASA missions.
Stellite
The go-to alloy for wear and corrosion resistance
While Inconel often dominates discussions on high-temperature alloys, Stellite is another high temperature alloy, but specifically designed for wear and corrosion resistance. Stellite is not just about withstanding high heat; it’s designed for environments where components face continuous abrasion, erosion, and the need to maintain performance under harsh conditions. From valve seats to cutting tools, Stellite is built for durability—but that durability also makes it a challenge to machine.
The origins of Stellite: From spark plug experiments to high-performance alloys
Stellite was developed by Elwood Haynes in the early 1900s while he was searching for a material that could resist corrosion in spark plugs. What he ended up with was a cobalt-based alloy that not only resisted corrosion but also remained incredibly hard and wear-resistant at high temperatures. The name “Stellite” comes from the Latin word stella, meaning star, a nod to the alloy’s luster and its resistance to tarnishing.
Where Stellite shines
Stellite’s properties are derived from its cobalt-chromium base, combined with stable carbides that provide extreme wear resistance. Unlike nickel alloys, which rely on a balanced microstructure of phases and precipitates, Stellite’s strength lies in its inherent hardness and the formation of carbides that resist abrasion and erosion. While some grades of Stellite are harder than others, they all resist wear and can operate at extreme temperatures.
Key Stellite alloys and their uses include:
- Stellite 6: For applications requiring wear resistance under both high heat and corrosion. Commonly used in valve seats, industrial bearings, and even surgical tools, Stellite 6 is hard to beat—literally.
- Stellite 21: Known for its improved thermal fatigue properties and corrosion resistance, Stellite 21 is often used in gas turbines and even in medical implants. It combines high hardness with enough toughness to handle repeated thermal cycling.
Why machining Stellite is a pain—and how to do it right
If you’ve ever tried to machine Stellite, you know it’s a challenge. The hardness that makes Stellite such a durable material also makes it nearly impossible to machine with conventional methods. Carbide tools are a must, and even then, you need low cutting speeds and plenty of cooling to prevent rapid tool wear. Successfully working with Stellite requires specialized knowledge and precision.
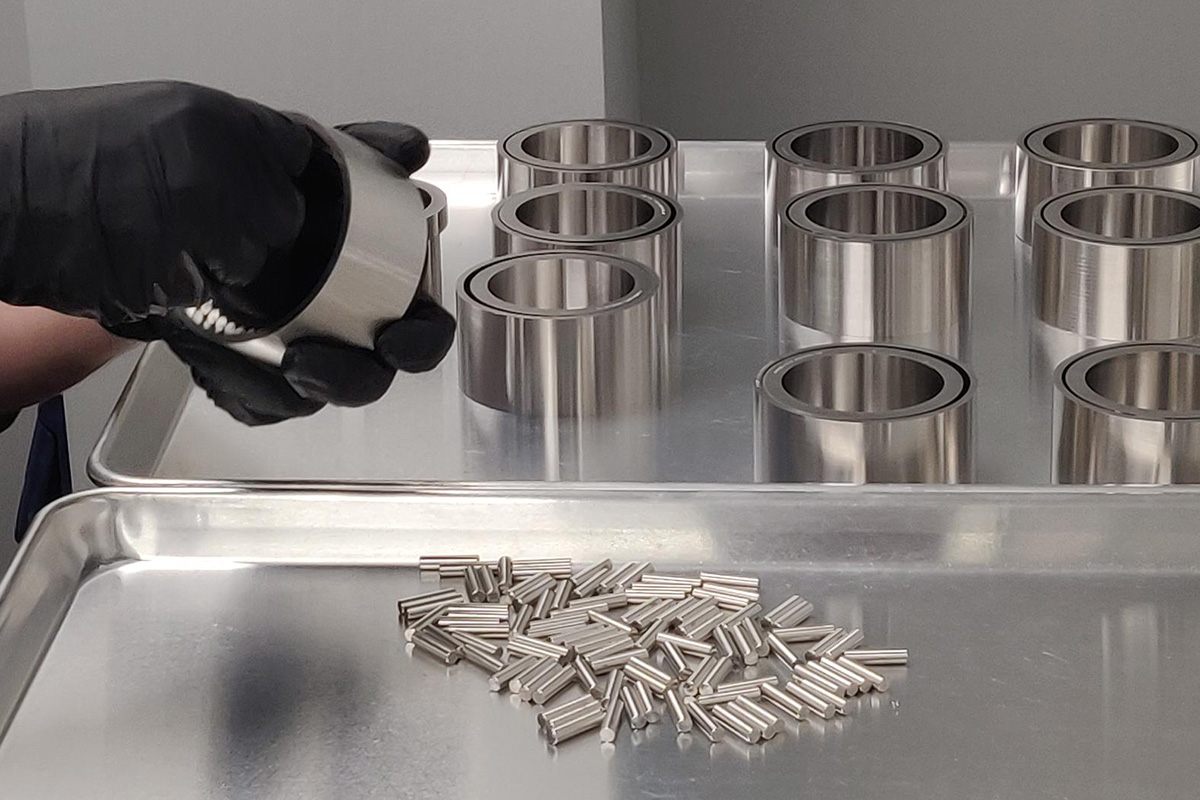
Stellite® roller bearings being loaded into empty races.
Conclusions
Superalloys are remarkable materials, blending cutting-edge metallurgy with the strength and durability needed for the harshest conditions. Whether it’s the high-temperature resilience of Inconel, the corrosion resistance of Hastelloy®, or the wear resistance of Stellite, each alloy brings something unique to the table—but those strengths also come with significant challenges in machining, fabrication, and cost management.
Selecting the right superalloy isn’t just about finding the highest strength or the best temperature resistance on a datasheet. It’s about understanding the trade-offs—between machinability and performance, between cost and long-term reliability, and even between availability and lead times. For example, Inconel may seem perfect for its heat resistance, but its machining demands can add substantial complexity. Stellite offers unmatched wear resistance, but only if you’re ready to handle its tough-to-machine nature.
Beyond Inconel and Stellite, there’s an entire world of high-performance alloys like Hastelloy, Nimonic®, and Waspaloy®, each designed for specific applications where failure is not an option. While we can’t dive into all their details here, it’s important to know that choosing the right material is only half the battle—you also need a partner who understands how to work with these alloys.
Our expertise, your advantage
This is where we come in. With deep experience across nickel, cobalt, and other superalloys like Nimonic and Waspaloy, we have the knowledge to get the best performance from these demanding materials. We know the pitfalls to avoid, the best machining and fabrication practices, and how to balance performance with efficiency. Whether you’re designing components for aerospace, energy, or chemical processing, we have the expertise to ensure your project succeeds.
We also recognize that every application is unique. We’re here not just to deliver parts, but to guide you through material selection and production from start to finish. When you work with us, you’re gaining a partner who understands the complexities of superalloys and can help you navigate them effectively.
Looking ahead: The future of superalloys
As industries continue to push the limits of performance, the need for advanced superalloys will only grow. Emerging applications, from cutting-edge jet engines to next-generation power plants, are driving innovation in both materials and manufacturing techniques. Advances in additive manufacturing, computational alloy design, and improved processing methods are shaping the future of these remarkable materials. Staying ahead in this field means not only keeping up with these trends but leading the way in applying them effectively.
Superalloys will remain crucial in solving engineering challenges that require materials capable of withstanding the harshest environments. And as these demands increase, having the right partner with proven expertise becomes more essential than ever.
In short, if you’re considering superalloys for your next project—whether it’s Inconel, Hastelloy, Stellite, or any of their specialized counterparts—you’re in the right place. We’re here to help you make informed decisions, avoid costly mistakes, and get the best performance from these extraordinary materials.