Selecting for Success
When it comes to critical parts—whether it’s bearings for high-temperature corrosive environments, mold tools, or performance automotive parts—getting it right the first time is non-negotiable.
Often you know exactly what you need and what materials meet the application requirements. But sometimes the best material isn’t clear, or you might be interested in a higher-performing option.
From tool steels to superalloys, we have the expertise to guide you toward the best material for your application and the know-how to machine it.
- Specialists in hard to machine, heat-resistant materials.
- Expertise in functionally-graded, multi-alloy components.
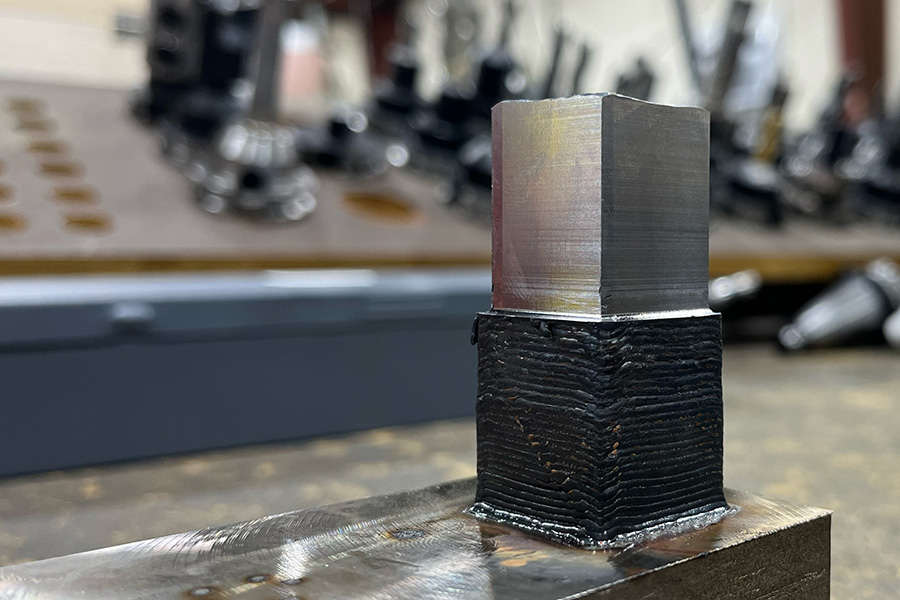
Materials & Properties
The following table demonstrates materials we can accommodate and relative property applicability.
Materials & Properties
The following table demonstrates materials we can accommodate and relative property applicability.
Material | Lightness | Heat Resistance | Corrosion Resistance | Hardness / Wear Resistance | ISO Group | Example Grades |
---|---|---|---|---|---|---|
Nickel | – | ISO S Heat-Resistant Superalloys |
Inconel® 625 Inconel® 718 Inconel® X-750 Hastelloy® C-276 | |||
Cobalt | – | ISO S Heat-Resistant Superalloys |
Stellite® 6 Haynes® 188 Ultimet® | |||
Titanium | – | ISO S Heat-Resistant Superalloys |
Grade 2 Grade 5 | |||
Stainless Steel | – | ISO M Stainless Steel |
304 316 440C 17-4H | |||
Carbon Steel | – | – | – | ISO P Steel |
1018 1045 A36 | |
Tool Steel | – | ISO H Hardened Materials |
H11 H13 M2 M50 T1 D2 | |||
Aluminum | – | ISO N Non-Ferrous Metals |
6061 7075 |
Materials & Properties
The following list demonstrates materials we can accommodate and relative property applicability.
Nickel
ISO S: Heat-Resistant Superalloys
Example Grades:
Inconel® 625 Inconel® 718 Inconel® X-750 Hastelloy® C-276
Lightness: –
Heat Resistance:
Corrosion Resistance:
Hardness/Wear Resistance:
Cobalt
ISO S: Heat-Resistant Superalloys
Example Grades:
Stellite® 6 Haynes® 188 Ultimet®
Lightness: –
Heat Resistance:
Corrosion Resistance:
Hardness/Wear Resistance:
Titanium
ISO S: Heat-Resistant Superalloys
Example Grades:
Grade 2 Grade 5
Lightness:
Heat Resistance:
Corrosion Resistance:
Hardness/Wear Resistance: –
Stainless Steel
ISO M: Stainless Steel
Example Grades:
304 316 440C 17-4H
Lightness: –
Heat Resistance:
Corrosion Resistance:
Hardness/Wear Resistance:
Carbon Steel
ISO P: Steel
Example Grades:
1018 1045 A36
Lightness: –
Heat Resistance: –
Corrosion Resistance: –
Hardness/Wear Resistance:
Tool Steel
ISO H: Hardened Materials
Example Grades:
H11 H13 M2 M50 T1 D2
Lightness: –
Heat Resistance:
Corrosion Resistance:
Hardness/Wear Resistance:
Aluminum
ISO N: Non-Ferrous Metals
Example Grades:
6061 7075
Lightness:
Heat Resistance: –
Corrosion Resistance:
Hardness/Wear Resistance:
ISO Material Groups
ISO Material Groups classify different metal families by their machinability to help categorize the techniques and tooling required to work with different alloys.
Understanding these groups helps machinists ensure high precision and longer tool life, and sometimes material knowledge can even help engineer a better product through judicious material selection.