Lose the Limitations
Combined additive and subtractive methods in one system.
Hybrid manufacturing leverages the advantages of each to efficiently produce complex, quality components that are too difficult or impossible to achieve with conventional manufacturing.
- Greater customization options.
- Disruptive technology that is seldom available outside of government or academic settings.
- Ideal for rapid prototyping of high-fidelity parts.
- Repair and refurbish existing components.
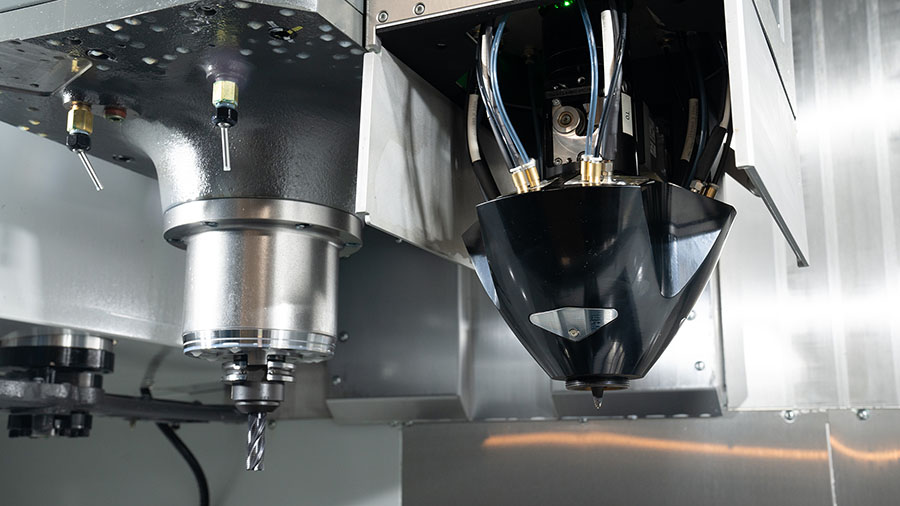
What is Hybrid Manufacturing?
Hybrid manufacturing merges additive and subtractive techniques into one system, leveraging the advantages of each to produce complex, quality components. It’s considered an advanced manufacturing method, bringing innovation, efficiency, and optimization to the production process.
The hybrid manufacturing process typically begins with additive manufacturing, where a 3D printer deposits or solidifies materials layer by layer to build a near-net shape. Excess material is then removed during the subtractive manufacturing phase using traditional machining techniques like milling, drilling, and grinding. This combination of additive and subtractive processes allows for increased design flexibility, less material waste, and accelerated production cycles.
Wire-Laser Metal Deposition
There are several types of metal additive methods that can be used in hybrid manufacturing, including wire-laser metal deposition (w-LMD), which is the preferred method of Hybrid CNC Parts.
With w-LMD hybrid manufacturing, welding wire is fed through print nozzles and melted by lasers. Hybrid CNC Parts w-LMD systems incorporate dual-head printers which allow for fast print times and seamlessly fabricated multi-alloy components.
The benefits of w-LMD over other metal hybrid methods—like powder-bed fusion or bound-filament printing—include fully dense parts, safer operations, and a diverse range of feedstock options, including high-performance materials like Inconel®, Invar®, and Stellite®.
Functionally-Graded Components
The metal 3D printers used by Hybrid CNC Parts are dual wire, able to accommodate two alloys simultaneously. Components with functional grading are useful for their enhanced mechanical properties, improved thermal performance, localized corrosion or wear resistance, and many more advantageous benefits.
Our process for multi-alloy components ensures proper integration of suitable materials for optimal functionality.
More information
Benefits of Hybrid Manufacturing
Hybrid manufacturing offers numerous advantages compared to conventional methods, including reduced material waste, shorter lead times, enhanced flexibility, and customization options. It is also ideal for the repair and refurbishment of high-value parts.
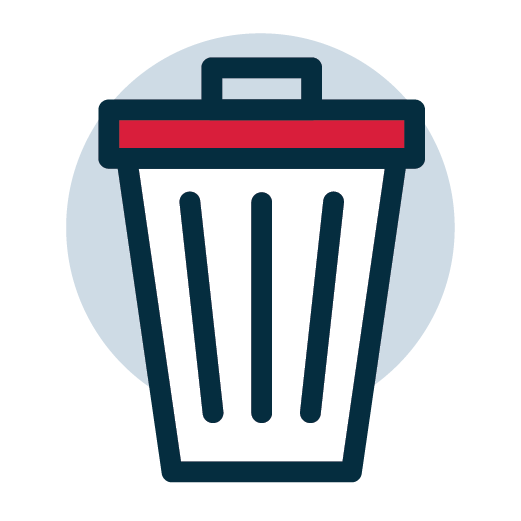
Less Waste
Significantly less material waste with material deposited only where needed.
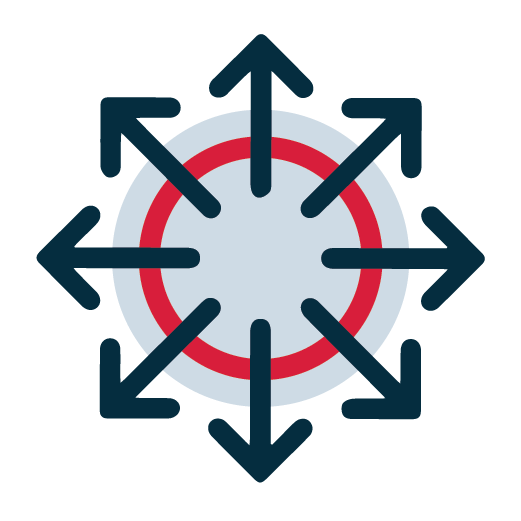
Versatility
Create, repair, modify, or enhance parts. Select from a large range of materials, including super alloys.
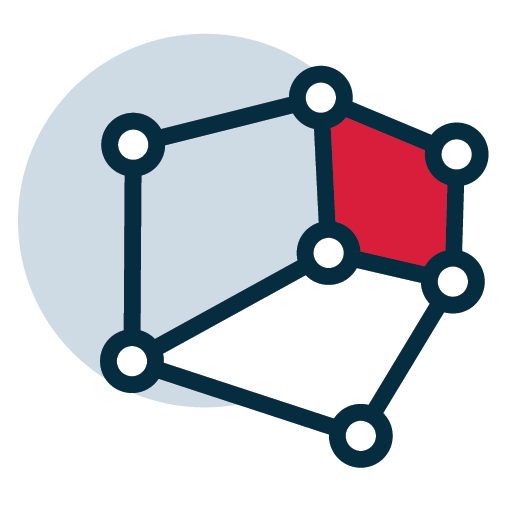
Complex Geometries
Ability to produce complex internal structures and intricate geometries. Near-net shape parts with minimal post processing.
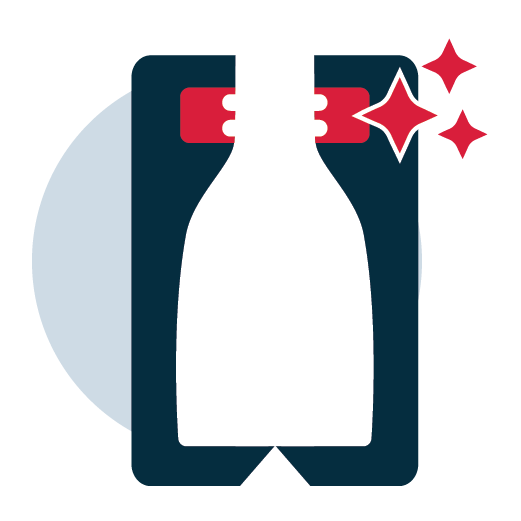
Enhanced Properties
Improved mechanical properties through material optimization and functionally-graded Alloy Composites.
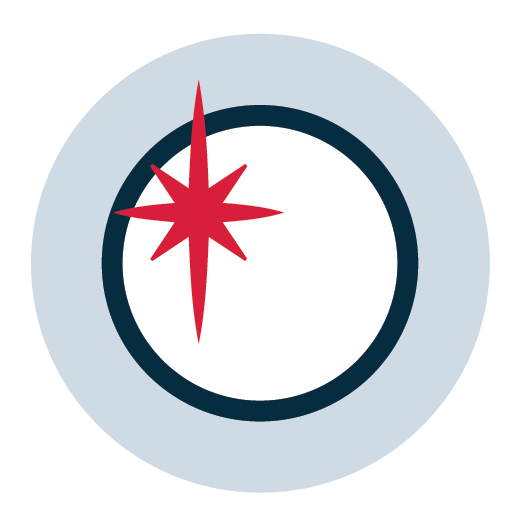
Surface Finish
High-quality surface finishes and tight tolerances.
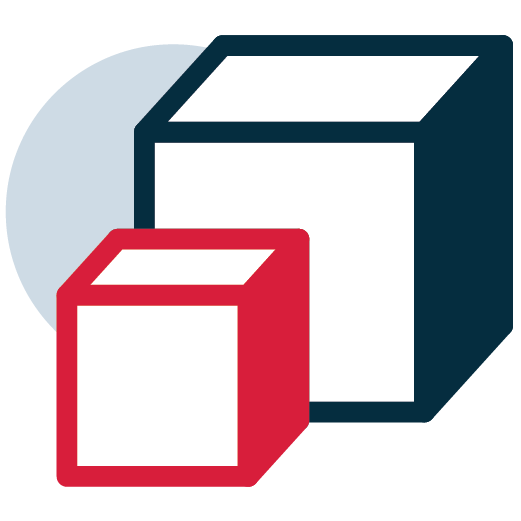
Easy Customization
Easy customization of parts without the need for new tooling.
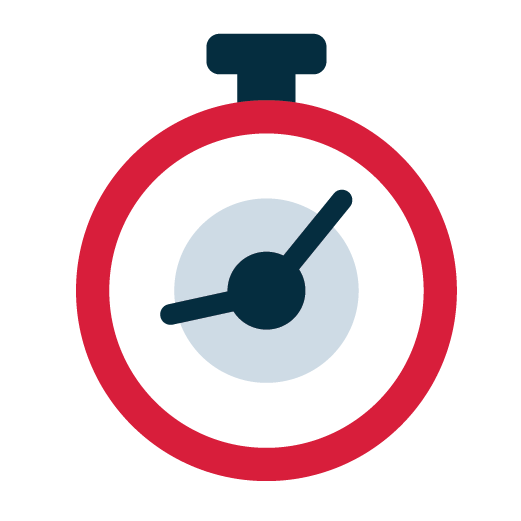
Reduced Lead Times
Faster production cycles with rapid prototyping, design iteration, and no extensive tool changes.
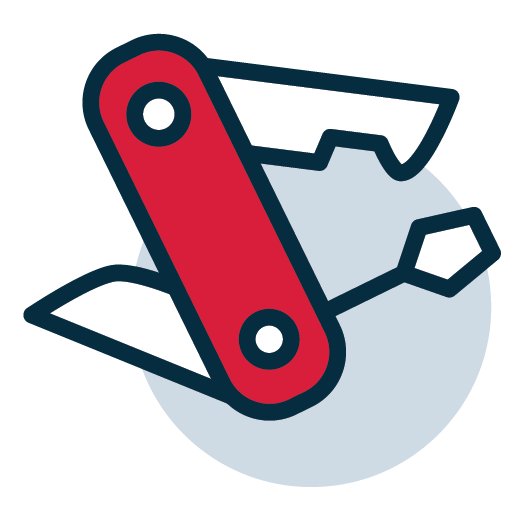
Integrated Functionality
Incorporate multiple functions and consolidate parts into a single component.
USE CASE
Extreme Environment Bearings
Nickel alloy (Inconel® 718)
These bearings were designed for NASA missions, where extreme environmental conditions are the norm. Temperature fluctuations, abrasive dust, corrosive atmospheres, and ionizing radiation are just some of the demanding conditions encountered.
We custom engineered Inconel® 718 bearings with enhanced mechanical properties and superior microstructure integrity, fabricated using w-LMD hybrid manufacturing. Inconel was chosen for its strength-to-stiffness ratio, high fatigue resistance, and ability to handle thermal expansion.
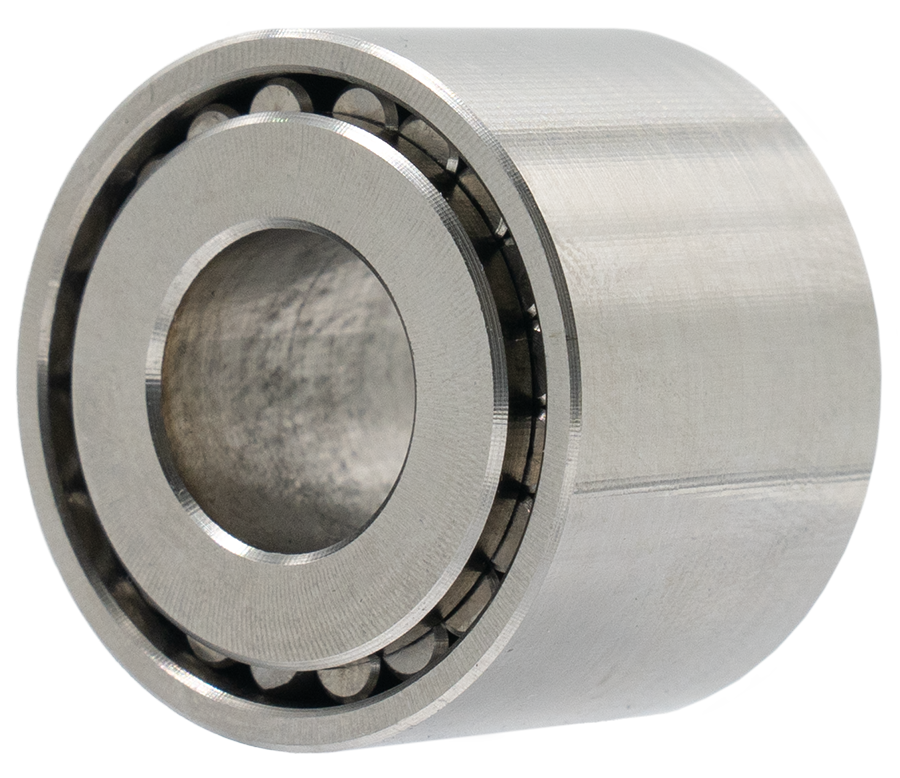